How 2025 Trends in Injection Molding Are Changing the Way Supply Chains Work
It’s time to talk about it. Being an engineer means we’re always in the hot seat, right? Get new ideas out quickly, make the product better, make it cheaper and don’t forget to ensure the supply chain doesn’t cause any issues. It’s going to be tough. We focus lots of energy on design, electronics and software, but what about plastic components? The enclosures, the gears and the connectors? Usually, that’s when injection molding is used and it’s a powerful manufacturing method that doesn’t always get enough attention.
Here’s what’s happening: injection molding is in the midst of a major transformation as we approach 2025. The sort of changes that change the whole process of making and delivering products, not just little improvements. Wouldn’t it be great if you could make your supply chain stronger, faster and less expensive, all by looking closely at how those plastic items are created? Intriguing, right?
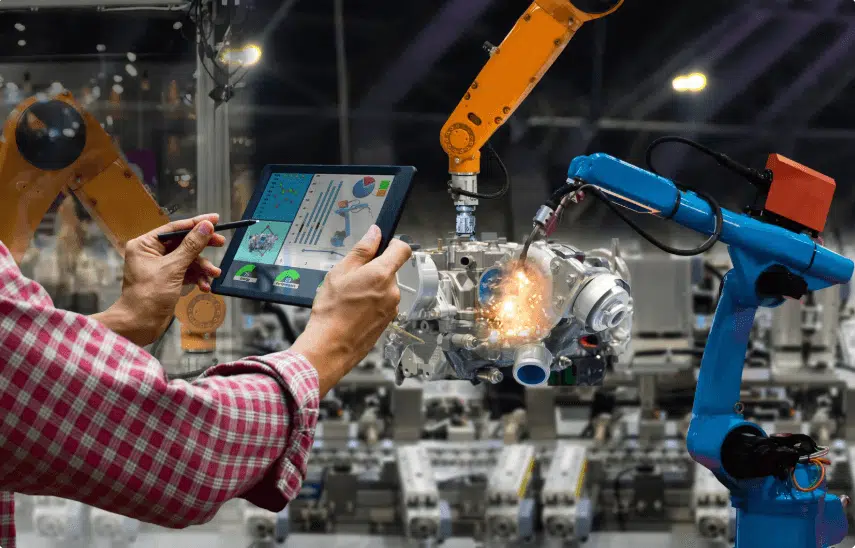
What’s Still Scaring Us: Supply Chains Are Still Causing Problems
Let’s be honest about this for a bit. The last few years haven’t been smooth for supply chains. It seems we all have a few gray hairs from paying higher shipping, waiting for products to leave ports and dealing with suppliers who go quiet on us. I kept feeling like I was smacking at different problems as they popped up. Long waiting periods, uncertain expenses, ongoing quality control issues and the constant fear about whether a supplier will let us down are the problems we can’t ignore. It could make you want to print all your parts yourself, but we realize that won’t work for the large number of parts required.
But imagine if I said that the plain injection mold which most people hardly notice, is quietly stepping up to take on these supply chain issues? I admit, that sound dramatic, but please keep reading.
Industry 4.0 is Helping Molding Become Smarter – It’s Not Just a Buzzword Anymore!
So much talk about Industry 4.0 these days that it’s hard to pay attention. I can see why. However, in the injection molding industry, it’s now becoming something concrete, something helpfully real. We could say we’re giving our molding machines a major brain improvement, with systems connected, lots of information and smart choices being made.
What does this practical change look like in factories in 2025?
We’re moving past the basic function of robotic arms into more advanced technology. We’re using AI-driven robots that complete challenging insert molding, detailed handling of parts and minor assembly, all through the day and night. We’re not taking jobs away from our workers; we’re giving robots the dull, hard work so our skilled technicians and engineers can improve the process, focus on quality and do real engineering. It’s similar to working with a tireless, highly efficient aide who lets you focus on the challenging parts of your work. The result? There’s less waiting and the results are much more dependable.
AI is helping with quality control in a major way. If we had sensors across the mold and the machine, they would be constantly sending temperature, pressure, flow rate and cooling data to an AI system. Now, machine vision can detect very small faults that people can’t spot after looking at parts for hours. Still, what really makes it special? Predictive quality. It can sense when a process is no longer within spec and bring it to your attention so you don’t make any defective parts. It’s even better if you can tell when maintenance is needed before something goes wrong. There would be a lot less waste, both in time and money, if we didn’t have to manage a huge pile of rejects or a sudden stop in the line. To be honest, it’s a huge improvement.
The Second Trend: Materials are Revamped – Sustainability Meets Practical Performance
It used to seem like using sustainable materials in plastics meant giving something up. It’s wonderful for the environment, but will it last? Is it expensive to buy? Do we think the product will function as it should in our current molds? All of these questions made perfect sense.
Ten years from now, the situation is totally different. Material scientists have been very busy lately. We’re noticing some truly remarkable improvements in:
- These days, bio-plastics and biopolymers aren’t the fragile materials they once were. We’re talking about PLA and PHA and other types of polymers from renewable resources that are now as strong or stronger than those made from fossil fuels.
- It is now much easier to collect, process and reuse both post-consumer and post-industrial plastics. For example, chemical recycling takes plastics apart, creating resins that are just as good as virgin resins. As a result, the idea of a fully circular plastic economy is now moving toward something that can actually happen.
- It’s great that designers are now considering how processable these materials should be. Today, a shorter cycle time or fewer mold changes isn’t as much of a problem as it was before. What effect does this have on your supply chain? Of course, hitting those goals and attracting eco-friendly customers is important, but that’s not all there is to it. You can also seek out different resins, save money as virgin resin prices go up and down and make your products more environmentally friendly. It’s just a smart way to do business. These things are obvious to customers.
Trend #3: Simulation and Digital Twins – Try It Out Before You Ever Start Building
If you’ve taken part in a long mold debugging process, you understand how difficult it can be. Every bit of back and forth, each adjustment and every trial means less time and more money spent. That’s where advanced simulation and the concept of the digital twin are now helping and it’s making a real difference.
This tool for analyzing mold flow has existed for some time and is excellent. Today, simulation software, supported by AI, looks at more factors than ever before. We’re concerned with:
- It is possible to design against warpage before the part is made, thanks to knowing how it will shrink and where stress will build up.
- This area has a big impact on how fast your process runs. Using simulation, designers can route conformal channels through the mold which removes heat much faster and more efficiently than simple drilled lines.
- Imagine if you could create a full simulation of your injection molding machine, mold and the specific material being used. You are able to run virtual trials, adjust process variables and observe the results, all at no cost for plastic or machine usage.
It’s a bit like seeing the future of your production line. You will notice if there are sink marks, weld lines or filling problems and be able to correct them online before they become costly and take a lot of time in the real world. If you can change and improve a design digitally, you can speed up the entire development process. Imagine the consequences of getting new products into the market more quickly.
Okay, that’s Interesting, But How Does This Better My Supply Chain?
That’s where the molten plastic and the steel meet which is the main part of the process. All the exciting trends are nice, but what do they really do to our biggest challenges: lead times, costs and risks?
I’ll explain this to you.
Getting Rid of Those Long Lead Times:
- The use of simulation reduces the number of required design and mold changes. Machining molds is now done more quickly with digital designs and automated CAM.
- Automation ensures that machines can operate at full speed all day and every day, if that is required. AI helps the process to automatically adjust settings as needed for best performance.
- AI does most of the inspecting and can keep up which means parts get through post-production faster.
There is a very big domino effect happening here. Producing goods in a way that brings them to market weeks or even months, ahead of schedule? Being able to handle sudden increases in demand instantly? That’s much more than a way to save time; it helps a company beat out its rivals. Huge.
I Found Some Significant Ways to Save Money.
- Less Waste: Fewer rejects are possible with the use of prediction and improved designs. That’s money you save right away from not using materials.
- Automation completes routine work, so your staff can focus on valuable activities. It’s really about raising jobs, not getting rid of them.
- Finding defects before items leave the factory and ideally solving them before they occur, prevents a lot of warranty claims, costs to fix and damage to a company’s reputation.
- Modern machines help reduce your energy bills. Improved processes and shorter cycle times result in using less energy to produce each part.
It’s not only about cutting costs a little; these technologies can make operations much more efficient. We’re looking at discovering savings opportunities you didn’t know were available.
Making the Operation More Durable and Safe from Risks
When those eco-friendly materials improve and their costs drop, you have a greater variety to select from. As a result, you can protect yourself from the ups and downs or lack of supply in the usual resin markets.
Better Predictions: With automation and AI, it’s easier to predict when maintenance is needed and production is more reliable. Trusting your production schedules is now a little less risky.
With advanced molding technologies being easier to use and more efficient, local or regional production can compete well against production in distant countries where labor is cheap. You might remember the delays and crowded ports that happened just a few years ago. It simply makes sense to include ways to keep that from happening. It is better to have shorter supply lines.
We Shouldn’t Overlook Getting Better with Suppliers:
Such technologies perform well when people collaborate. This means passing along more design and data information between product engineers and the people who are making your molds.
If your molder is using AI-based QC or advanced simulation, they’re not only your supplier; they’re also helping you achieve your goals. They might introduce ideas you haven’t thought of before.
It’s no longer enough to work with suppliers who are not embracing these 2025 trends; you need to move forward with those who are. It’s not only about deals, but about forming relationships with people who share your progressive ideas.
It’s Easier Than You Think to Get Started
Let’s take a moment to breathe. If any of this sounds exciting but you don’t know where to begin, The equipment my suppliers use is as old as the dinosaurs! That’s certainly a valid idea. It can seem as if bringing in new technology is just as hard as boiling the ocean.
It’s good news: you don’t have to handle everything all at once.
Talk with your existing injection molders to learn more. What do they notice around them? What do they plan to do about adopting some of these new technologies? There might be things you didn’t expect.
One area to concentrate on is enhancing your initial design analysis by using stronger simulation resources. Maybe start with a small project to test out a couple of sustainable materials for a part that isn’t important.
Learn (and Have Your Team Learn) About These Things: There is plenty of information available. To learn more, check out industry webinars, online trade shows (which are improving fast) and the publications from Gardner Business Media such as Plastics Technology and MoldMaking Technology.
It’s not just a quick fix to invest in these areas or team up with suppliers who are. It’s focused on preparing for the future and making the company more robust. The edge it has will continue to improve.
Building the Future by Creating Quality Parts
The truth is, injection molding now plays an important role throughout the entire product process. Thanks to smart automation, AI in quality control, great new materials and simulation, manufacturing is now a major strategic advantage. Something that can change how quickly your supply chain works, how much it costs and whether it survives hardships.
These changes aren’t only something we need to match; they drive us to lead the industry. It’s focused on improving products, bringing them to customers sooner and doing so in a smarter way. As a result, the main concern is how these trends will improve supply chains – they already are. The question becomes, how will you make use of their support?