China Plastic Mold and Injection Molding Cost
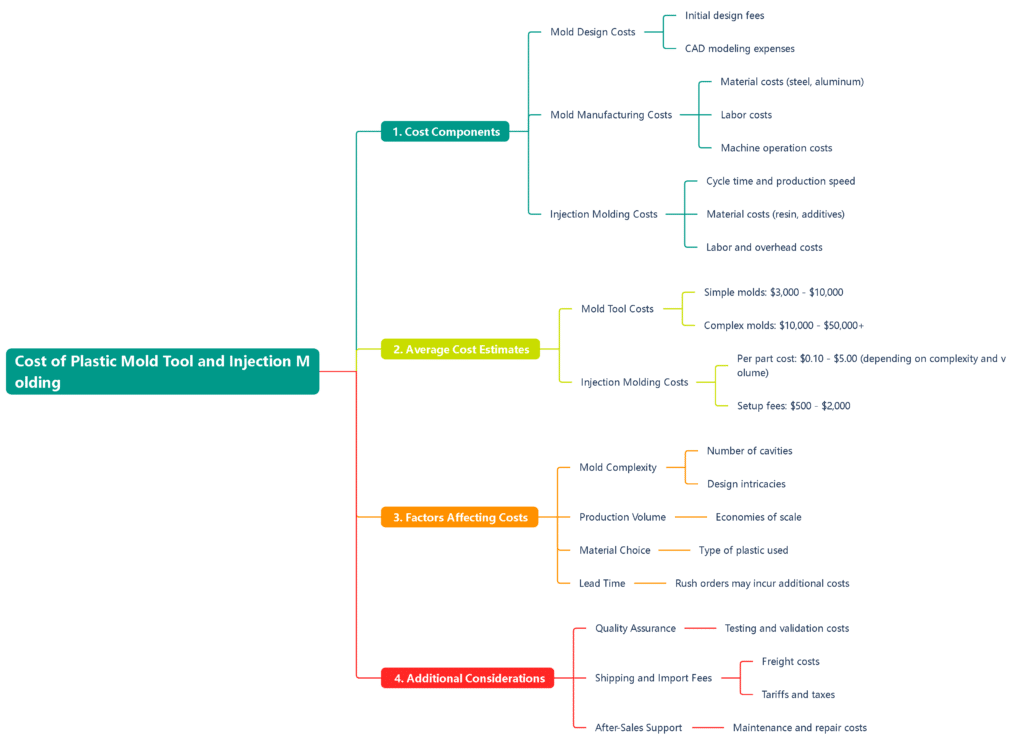
what is Real Cost of Injection Molding: A Complete Guide
Injection molding provides a production cost range from $1 to $5 per unit at high production volumes (10000 pcs per batch),and its initial mold costs start from $2,000 to $20,000. The production technique enables both high quality and economical mass manufacturing capabilities.
Key Cost Components:
- According to research mold design together with creation expenses account for between 60-70% of startup expenses. The new technology from our company enhances mold production which cuts down initial capital expenses by 15%.
- Unit costs vary by 30-40% based on the selection of materials according to Material Selection and Cost Testing data. Our up-to-date data system optimizes material consumption which leads to a minimum waste reduction of 12%.
- Our Production Volume Analysis Studies show that manufacturing larger product quantities leads to lower unit price costs. The production of 100,000+ units enables cost reduction to under $1 per piece form some items.
Cost Comparison Table:
Production Method | Initial Cost | Unit Cost (100k+) | Quality | Speed |
---|---|---|---|---|
Injection Molding | $3k-20k | $0.5-5 | High | Fast |
3D Printing | $0.8k-5k | $5-20 | Medium | Slow |
CNC Machining | $1k-10k | $10-50 | High | Medium |
The market shows that injection molding expenses have reduced by 15% during the past five years because of technological enhancements and automated systems. The optimal production cost efficiency comes from running production at least 10,000 times according to expert analysis.
Injection molding is a really useful manufacturing method for making parts. It works by injecting melted stuff into a mold. The melted stuff can be metals, glasses, rubbers, or commonly something like plastic.
The way it works is, first the right material gets melted in a heated barrel. Then it gets injected at high pressure into the mold cavity, which is cooled. The material takes the shape of the cavity as it hardens, while the sprues and gates get removed from the part.
- China Plastic Mold and Injection Molding Cost
- history of injection molding
- cost of plastic mold
- cost of injection molding
- tips to reduce injection molding cost
- Consider opting for soft tooling
- Use a more efficient plastic resin
- Simplify Your Design
- Design More Efficient,longer-lasting and possible multi-cavity molds
- Reduce The Cycle Time
- Automate repetitive tasks and processes
- Utilize Parts Or Models Which Are Already Available
- Build New Models That Are Male Shaped
- Adopt Flat Runs-Outs
- Choose Supporting Structures Wisely
- Fillers Added
- Reduce Scrap
Injection molding is one of the most popular ways to make plastic parts because it’s fast, efficient, and really versatile. Injection molded stuff can range a lot in size and complexity, and gets used in tons of industries from medical to cars.
history of injection molding
Injection molding is a great manufacturing process for making parts by squirting melted material into a mold. It was invented back in 1872 by this German engineer dude named Arthur Eichengrün. Eichengrün was a German engineer working on a way to make metal parts using heat and pressure. He figured out he could inject melted material into a mold and it would cool and harden quickly.It started getting used a whole lot in the 1970s. Injection molding is used to make all kinds of products, from medical gadgets to toys.
Eichengrün’s invention changed manufacturing, since it allowed mass production of parts with complex shapes. Injection molding quickly got popular in a bunch of industries, including cars.
Lots of people who purchase injection molds from China just care about saving money. But that’s not the right attitude, since you really want a mold that works right and is reliable instead of just being cheap.
cost of plastic mold
Injection molding stands out as a practical manufacturing process, giving life to plastic parts and components in an efficient manner. The swiftness and effectiveness of injection molding shine through as it churns out top-notch parts without breaking a sweat. But, let’s be real, this method does come with a price tag. The cost associated with injection molding is a mixed bag influenced by various elements – the plastic variant being used, the part’s dimensions, how intricate the design is, and the quantity you’re eyeing.
When you take all these factors and put them on the scale, it becomes clear that opting for injection molding from China can be a smart move, provided you keep a few things in the back of your mind.
It’s not rocket science that the price of injection molding hinges on the kind of mold you’re dealing with. Simpler molds, usually crafted from aluminum or steel, won’t burn a hole in your pocket like their intricate counterparts made from fancier materials. Mold size? Oh yeah, that’s in the mix too. Bigger molds gobble up more material and money during their creation. Now, let’s talk design complexity. The fancier your design, the more TLC it demands during fabrication, possibly even requiring snazzy add-ons like cooling channels or ejection pins.
mold cost breakdown
Item | Percentage | |
1 | Steel Material | 20-35% |
2 | Machining(CNC,engraving) | 25-40% |
3 | Assembly(bench work) | 15-20% |
4 | Mold design | 5-10% |
5 | Tax, profit | 20-30% |
To determine How much a plastic mold tool and injection molding, some factors are considered:
Complexity of Parts:
When it comes to injection molded parts getting more intricate, there’s a ripple effect that can’t be ignored. Wrangling with this complexity brings forth a notable challenge – ensuring that every nook and cranny in the mold gets its fair share of the action. Things get tricky, especially when those parts sport an array of tiny, intricate features.
Speaking of intricacies, even a small sidewall undercut can send shockwaves through the mold’s structure, leading to a heftier bill. Brace yourself for a pocket pinch of at least $500. That’s not all – the mold will beef up in size and demand some extra rounds of heat treatment.
Counting the Cavities:
Ever heard of multi-cavity molds? They’re like the budget-saver’s secret weapon. How? Well, picture this: two or more parts, similar or not, getting molded in a single tool cavity simultaneously. It’s the nifty way to cut back on individual mold costs and keep your budget in check. Basically, fewer tools needed for the same project – smart, right?
Narrowing Down Tolerances:
Let’s talk dollars and cents in the world of injection molding. Tolerances – they’re like the hidden cost whisperers. The rule of thumb is: the tighter the tolerances, the deeper you dig into your wallet for that mold. If saving a few bucks is your goal, here’s a tip: ease up on the tolerances a bit. But here’s the catch – you don’t want parts that are too loose and wobbly. It’s like a delicate dance to strike the perfect balance and save those hard-earned bucks.
Choice of Tooling Materials:
Steel – the heavyweight champion of injection mold materials. No doubt, it’s tough as nails and built to last. Trouble is, it can put a dent in your budget. Enter aluminum, the wallet-friendly contender with great thermal conductivity. Yet, it’s not as resilient as steel and might show signs of wear sooner. Then there are the composite materials like carbon fiber and fiberglass, offering a blend of strength and affordability. But remember, they might not withstand the test of time as steel does.
Unveiling Cam Mechanisms:
Ever wondered how molds morph shapes? Cam mechanisms are the magicians behind the scenes. We’re talking sliders and lifters – the MVPs of mold movement. They’re a versatile bunch, conjuring up all sorts of shapes and designs. But, hold your horses, they’re not cheap tricks. These bad boys can pack a financial punch.
Tool Longevity:
Here’s the scoop on tool life: the frequency of use matters. A high-priced mold that’s brought out on rare occasions enjoys a longer lifespan, thanks to less wear and tear. Delicate tasks also play a role – tools used for intricate work age more gracefully than those tackling heavy-duty jobs.
Resin Quality and Aesthetics:
Let’s talk resin – it’s the grade that gets the spotlight. The dance between resin grade and the injection part’s demands shapes the mold choice. And don’t forget aesthetics – the look and finish of your piece. Higher purity means a heftier price tag, but if looks are your priority, you might need to compromise. Want a top-notch finish? Dig deeper into your pockets. But if rustic charm is what you’re after, a more affordable mold can do the trick.
These costs are spread out over the number of parts being made, but the real cost includes the time needed for molding and actually making the parts.
So a hot-runner tool might be pricier at first than a two-plate tool, but you save money by not needing someone to manually remove parts from runners since the part cost can be lower with the hot-runner.
Purchasing folks shouldn’t be fully in charge of buying tools – there’s too many factors they might not get. Tools should be specified upfront. The goal is getting the lowest cost tool that can properly make the parts to spec, as done by experienced mold makers.
When getting a mold, it’s important to address key areas of interest. The mold design checklist and injection mold spec sheet cover these areas.
Early on when developing a product, the design and sales teams should consider mold costs, production costs, and the final part price.
This lets management decide direction. Estimating mold costs isn’t hard, but you should talk to everyone involved.
If you want a quote for tooling, you should have the preliminary design, final drawings, and a sample part if possible.
Part drawings and specifications should include the following information:
- Dimensions that determine the complexity of the cavity and part tolerances.
- Various essential surface finishes required.
- The requirement for tight tolerance as well as the number necessary.
- In square inches, the area covered by the part’s length and width.
- All functions that operate within the mold (caming, unscrewing).
- Tolerance-based tooling requirement balance.
- Resin used to form the part.
- Tolerances and part volume should determine the number of cavities.
- Different types of tools include two-plate, three-plate, hot-runner, etc.
After answering the above questions, decide on the number of materials and standard components to be used and calculate costs from the suppliers’ catalogs.
Mold makers must prepare a list of understandable manufacturing processes and assembly processes and the various items involved in production;
- these must include the cavity(ies),
- the cooling requirements,
- the location of cooling lines around the cavity, the ejector system,
- and any other operational procedures required.
Figure out how long each step takes, and what the hourly rate is for each step. Add in any outside costs for heat treating, finishing, polishing, textures, etc. to get a sense of everything needed.
The purchasing team can be more efficient and accurate by getting this info. It allows them to better evaluate and budget for a specific job.
First-time mold buyers, especially those unfamiliar with mold design, often struggle gathering all this. The wage rates and time estimates will just be guesses.
It’s important to get the exact costs from suppliers for any new equipment.
By specifying how the tooling quote should be prepared, the buyer can get details like a breakdown of parts, functions, and timelines.
For simple molds, design costs can range from $3,000 with minimal changes to $7,000 with constant tweaks. For a basic job, design is 5-10% of total cost.
It usually takes 4-10 weeks to design, machine, build, finish and test a mold for injection molding. To avoid shipping the mold back and forth, use a tooling company that can also do the injection molding.
The best way to learn mold estimating is talking to mold builders who make similar size and complexity molds.
Look at their work quality, equipment, processes and services offered.
Get quotes from tool builders and mold owners. If no mold builders available, may need to contract a molder. Here, being able to fully describe the part requirements is key.
This process can avoid extra costs and result in even lower per-part prices. With these capabilities, the mold costs more initially but saves on each part long-term.
cost of injection molding
The cost of injection molding will depend on a number of factors, including the size and complexity of your part, the type of plastic being used, and the quantity being made. In general, it costs more to manufacture small quantities than large quantities.
Why those important for injection molding cost
- Part size- bigger parts mean a bigger mold, which means that bigger steel will increase the steel cost for the injection mold.
- Part design- the more complex a part is, the more detailed the mold has to be. Some complicated parts will require special features to be added, such as lifters or sliders. Therefore, you should be open to advice from your mold maker and see if there’s anywhere that you can alter the part design to save on injection mold costs.
- Materials: Depending on the part material of choice, the injection mold will have to be made of a particular material. For instance, if corrosive plastic-like PVC is to be used, the mold will have to be stainless steel to avoid any damage, ultimately bump the price up.
- Part finish requirements- where parts have high gloss surface requirements, then more expensive steel and precise technical polishing will be vital, adding to the price.
- Production volume- higher volume molds need more cavities, and so the mold will be larger. They also require a higher steel grade to last for longer, which impacts the injection mold cost.
- Country of manufacture- different countries have different wage rates. If your mold is made in a country where labor costs are low, then you’ll naturally save money. In China, the average cost of an injection mold is around 40% less than in western nations.
tips to reduce injection molding cost
Here are some great tips to ensure that your organization’s costs remain as low as possible:
Consider the viability of opting for soft tooling
Soft tooling presents a more cost-effective alternative to hard tooling, which involves crafting molds from steel or aluminum. Instead, soft tooling leverages materials like polyurethane or other flexible substances, which are not only more economical but also offer enhanced adaptability. This method is particularly favored among manufacturing firms that lack extensive experience in injection molding. It proves advantageous for scenarios involving low-volume production runs and prototype creation. Moreover, soft tooling boasts a commendable cost-efficiency and demands a reduced lead time compared to its hard tooling counterpart.
Enhance cost-effectiveness through judicious selection of plastic resin
Different plastic resins come with distinct attributes that significantly influence the potential to curtail injection molding expenses. Some resins are tailored for high-volume applications, while others cater to low-volume manufacturing needs. Another avenue for cost reduction involves incorporating recycled plastics within your molds, which can yield further financial benefits.
Key to lowering injection molding costs is the careful choice of materials that exhibit lower energy consumption during the melting and cooling phases. This is especially pertinent when dealing with multi-color processes or intricate mold structures.
For instance, if you’re currently utilizing rigid PVC material characterized by thick walls—resulting in heightened energy consumption—consider transitioning to alternative materials like ABS or PP (polypropylene). Both these options boast thinner walls, thereby minimizing energy requirements during both the heating and cooling stages.
Streamline your design approach
Crafting an elaborate, fully dimensioned drawing for mold design isn’t always imperative. Simplifying the process can be accomplished through a basic sketch accompanied by textual descriptions of each component, along with a part print. This streamlined approach is an initial step towards cost reduction, efficiently reducing the workload and expenses associated with CAD processes.
The geometric intricacy of your part constitutes a pivotal factor influencing injection molded part costs. Complex geometries necessitate greater design efforts and longer production times. Furthermore, they augment expenses related to tooling and molds, attributed to their intricate nature.
Moreover, parts characterized by thicker walls entail higher material consumption, amplifying their overall cost.
Optimize the fabrication of drill jigs used for shaping holes in sheet metal parts via glass-reinforced plastic (GRP) laminates. Typically, a representative part is created after drilling all holes in their precise locations. This tool can be accompanied by a variety of instructions, ranging from freehand sketches to written guidelines specifying part dimensions and quantities of required drill bushings.
Design More Efficient, Longer-Lasting and Possible Multi-Cavity Molds
Injection molds are constructed from metal and will eventually deteriorate. The more usages, the quicker the wear. Costs can be lowered by designing longer-lasting molds, utilizing materials that do not erode as rapidly (aluminum vs. steel) and using titanium or nickel alloys for stronger machinery components.
Injection molds come in various shapes and sizes, from simple straight-sided parts to intricate parts with overhangs and cavities. The more complex the part, the more costly to construct. This expense can be reduced by building simpler molds that utilize less metal.
Injection molding employs extremely high temperatures and pressures that can degrade the mold over time. If a durable product is designed and production is straightforward, waste can be minimized and money saved long-term. For instance, if multiple identical parts are required, consider a multi-cavity mold instead of a single-cavity mold.
Reduce The Cycle Time
The injection molding cycle time is the duration to complete all steps to produce one unit. A typical cycle includes:
Feeding material into the hopper
Heating and melting the material
Filling the mold cavity with molten plastic
Cooling and solidifying the part
Opening the mold to eject the finished product
Cycle time is one of the most crucial cost factors, as faster production allows more parts in a given timeframe, reducing per-unit costs. Injection molding cycle times vary substantially depending on part complexity and tool size.
Automate Repetitive Tasks and Processes
Automating the injection molding process can provide cost savings in several ways. First, it enables producing more parts with less labor – meaning smaller staffing and payroll costs. Additionally, automation increases efficiency by reducing cycle times. This means less downtime between runs, saving on labor and materials. Finally, automation reduces employee injury risk from repetitive tasks. Although initially costly, automation can improve the bottom line long-term.
Utilize Existing Parts or Models
Essentially, plastics are a replicating material, requiring a form except in special cases like loft templating. The fastest plastic replication method is mimicking an existing design like a model or prototype.
Build New Models That Are Male Shaped
When designing a master model, construct it for fastest duplication, commonly in a male shape, using the minimal metal thickness.
Adopt Flat Run-Outs
Engineers strongly recommend maximizing flat run-outs where constructed, as they provide the simplest structures.
Choose Supporting Structures Wisely
Every support structure type has advantages and disadvantages. Wood is light and inexpensive but dimensionally unstable. Cast iron is similarly priced but requires lengthy machining. Aluminum casts are more expensive but can be machined quicker. Cast steel is strongest but takes the longest and is most costly.
Fillers Added
Where large plastic quantities are needed without strength, fillers can increase performance cost-effectively. Adding fillers also increases plastic part hardness and stiffness, especially useful for high-strength, durable components.
Fillers like clay, calcium carbonate, limestone, and aluminum oxide are commonly used.
Reduce Scrap
Scrap is a major cost contributor. Quality issues cause defects, production/delivery delays, and higher scrap rates. Quality control systems like laser inspection can catch defects before they become problems, reducing scrap and costs.
Overall, sourcing quality injection molding services can improve profitability. But costs must also be controlled.