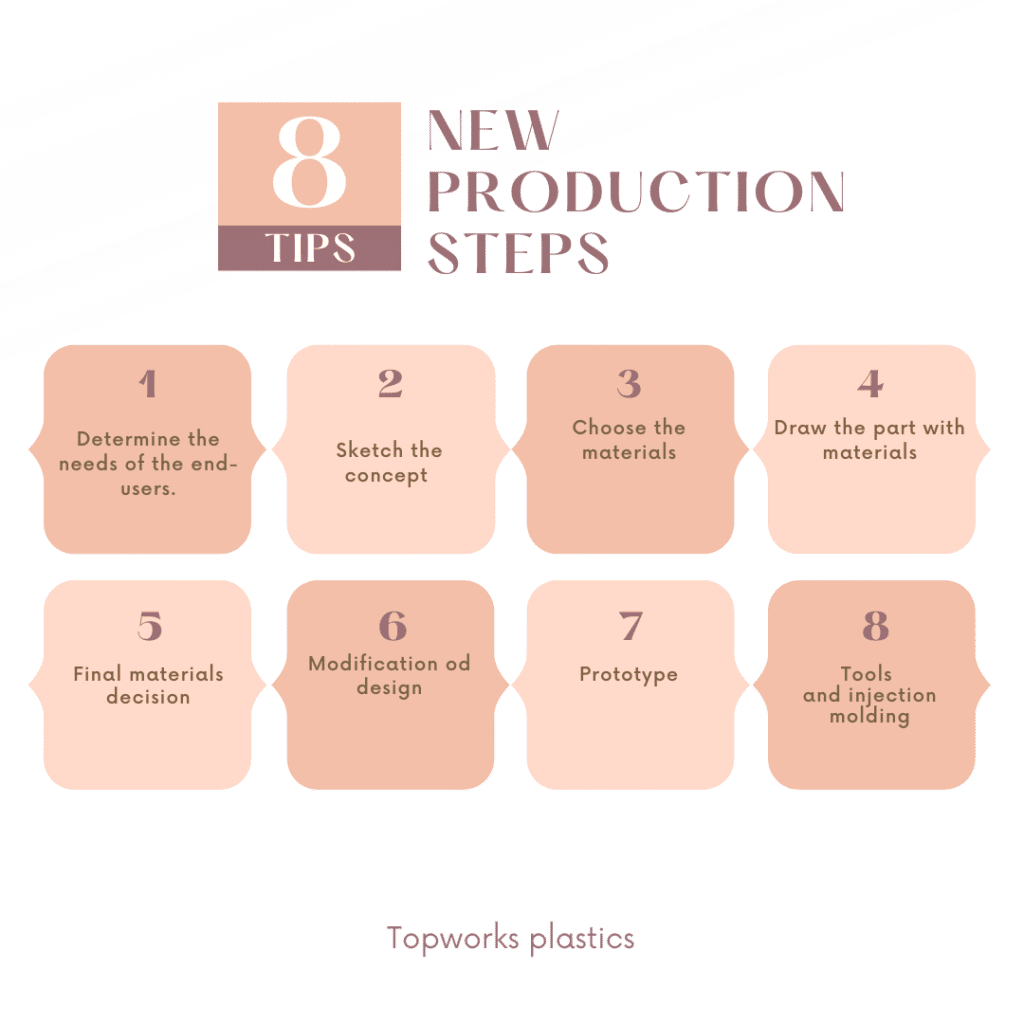
The Ultimate Guide to Simplifying the Design Process for New Product Developers
Creating a new product is both an exciting and daunting task. Whether you’re a seasoned designer or a new product developer, the journey from concept to production requires precision and a well-organized approach. The design process can be broken down into 10 key steps, each integral to ensuring your product is both functional and manufacturable. By understanding and following these steps, you can streamline your workflow and avoid costly mistakes along the way. Let’s explore these steps in detail.
1. Defining Requirements
The first and most crucial step in any design project is defining the requirements. This stage involves determining the product’s primary function, target market, and user needs. A detailed set of requirements guides the design process and keeps everyone on the same page.
For example, when designing a new consumer electronics product, you might consider factors such as size, weight, and battery life. The more specific you are, the easier it will be to align your design decisions with the goals of the product. It’s important to keep an open line of communication with all stakeholders, as their feedback can help refine the product vision and define features that will differentiate the product in the market.
2. Create a Preliminary Concept Sketch
Once you’ve defined the product requirements, it’s time to start thinking visually. Creating a preliminary concept sketch is often the first step in the design phase. At this stage, your sketch doesn’t need to be precise—just a rough representation that helps communicate your vision. This sketch acts as a tool for identifying potential issues early on.
For example, if you’re designing a housing unit for an electronic device, a rough sketch can highlight whether the internal components will fit together and whether there’s sufficient space for heat dissipation. The sketch helps you catch problems that might not be obvious in abstract descriptions. Once the concept is solid, it can lead to more detailed designs and 3D modeling.
3. Initial Materials Selection
At this stage, you need to consider the materials you’ll use in the final product. Materials selection is essential not only for functionality and durability but also for manufacturability. Different materials offer various benefits, such as strength, flexibility, resistance to heat, and ease of molding.
If you’re designing a product with a plastic casing, for instance, you’ll likely use injection-moldable thermoplastics like ABS (Acrylonitrile Butadiene Styrene) or polycarbonate. ABS is often chosen for its strength, impact resistance, and ease of injection molding, which makes it ideal for consumer electronics housings. Understanding material properties helps inform your design decisions—how thick should walls be? Will the material be able to withstand repeated use? These questions guide your decisions early in the design process.
General Purpose Polystyrene | PS | Lampshade, instrument housing, toys, etc. |
---|---|---|
Teflon, PFA | Chemical fittings, mechanical parts | |
ETFE | Chemical fittings, mechanical parts | |
Acrylonitrile Butadiene Styrene | ABS | instrument housing,House ware, advanced toys, sports goods |
Acrylonitrile Styrene | AS(SAN) | Daily transparent containers |
Acrylonitrile Styrene acrylate copolymer | ASA | Outdoor furniture,car outer mirror housing |
Butadiene Styrene | BS(BDS) | Special packaging, food containers, pen, etc. |
Cellulose Acetate | CA | Tool handles, containers, etc. |
Cellulose Nitrate | CN | Spectacle frames, toys, etc. |
Chlorinated Polyethers | PENTON( CPT) | Substitute for stainless steel |
Chlorinated Polyethylene | CPE | Building materials, pipe, cable insulation layer, heavy packaging materials |
Chlorinated Polypropylene | PPC | Daily necessities, electrical appliances, etc. |
Edit | ||
Ethyl Cellulose | EC | Tool handle, sports goods, etc. |
Ethylene-Propylene Copolymer | FFP | High frequency electronic instruments, radar insulation components |
Ethylene-Vinyl Acetate | EVA | Soles, film, sheet, tube, daily necessities, etc. |
High Density Polyethylene | HDPE | Packaging, building materials, buckets, toys, etc. |
High Impact Polystyrene | HIPS | House ware, electrical components, toys, etc. |
Low Density Polyethylene | LDPE | Packaging bags, plastic flowers, plastic bottle, wire, packaging etc. |
Methyl Methacrylate-Butadiene | MMB | Machine frame, frame and daily necessities, etc. |
Perfluorinated | ||
Poly(Butylene Terephthalare) | PBT | |
Poly(Ethylene Terephthalare) | PET | Bearings, chains, gears, tapes, etc. |
Poly(Vinyl Chloride) | PVC | Bar, pipe, plate, pipe, wire insulation, sealing, etc. |
Polyamide-1010 | PA-1010 | Rope, pipe, gear, mechanical parts |
Polyamide-6 | PA-6 | Bearings, gears, tubing, containers, daily necessities |
Polyamide-66 | PA-66 | Machinery, automobile, chemical, electrical equipment, etc. |
Polyamide-9 | PA-9 | Mechanical parts, pump, cable jacket |
Polycarbonate | PC | transparent parts, resistance to impact parts |
Polychlorctrifl uoreethylene | PCTFE | Transparent mirror, valve fittings, etc. |
polyethersulfon e | PES | Electrical parts,aircraft and automotive parts, etc. |
Polymethyl Methacrylate | PMMA | Transparent decorative materials, lampshade, windshield, instrument case |
Polymethyl Methacrylate-Styrene | MMS | transparent products with heavy loading |
Polyoxymethylen e(Polyformaldeh yde) | POM | Good abrasion resistance, for mechanical gear, bearings, etc. |
Polypropylene | PP | Packing bag,packaging, daily necessities, toys, etc. |
polysulfone | PSU(PSF) | Electrical parts, aircraft and automotive parts, etc. |
Polytetrafluoro ethylene | PTFE | High frequency electronic instruments, radar insulation components |
4. Design Parts
With your material selection in hand, it’s time to design the parts that will make up your product. This step is crucial because each material behaves differently. The way a thermoplastic like polyethylene expands when heated is quite different from how metals behave.
In injection molding, for example, the design needs to account for the material’s shrinkage during cooling. If you don’t account for this, you could end up with warped or misshapen parts. A good practice is to include features like draft angles in your design, which help with easy removal of the part from the mold. The more you align the design with the material properties, the easier and more cost-effective the manufacturing process will be.
Here is a summary table for injection molding design considerations:
Design Aspect | Considerations |
---|---|
Wall Thickness | does your design meet or exceed the nominal wall thickness? With a consistent wall thickness in the design, will your part cool evenly? |
Draft Angles | What’s your draft angle to the shrinkage you expect during cooling?Can your part be ejected from the mold easily with the draft angles you have? Are you going to stress your mold with your current design? |
Corners | Have the corners been radiused to avoid shrinkage, warping, shearing and/or breakage?How are all corners shaped in the mold so enough material can flow in and a consistent wall thickness is maintained? |
Undercuts | Can you remove any undercuts from the mold design without changing the function of the part?Can the mold be designed to accommodate the undercuts without going over budget? |
Resin Selection | Does the part design allow for proper flow of resin during injection and will it withstand the pressure required? What can affect the part’s cooling time, finish or other properties? How can you resolve those with changes to the part design and/or resin? |
Tolerances | How do your part’s tolerances affect the tooling (i.e. changing material for the mold, needing extra quality checks or more complex molds)? How can you address the performance requirements by redesigning the part/mold? |
5. Structural Analysis
Structural analysis is one of the most critical steps in the design process. Without it, your product may end up failing under real-world conditions, which could lead to costly recalls, delays, or even a damaged brand reputation. The goal here is to predict and analyze how the product will behave when subjected to various forces, environmental conditions, and stresses.
For example, when designing an injection-molded plastic component, the material’s structural integrity is paramount. Certain materials, like polypropylene (PP), might behave differently under stress compared to materials like polycarbonate (PC), which is much more rigid and durable. Using Finite Element Analysis (FEA) software, engineers can simulate how the part will respond to pressure, temperature changes, and mechanical forces. FEA helps identify weak spots in your design, such as potential points of failure or areas prone to warping under heat or stress. This analysis is especially important for products that will be subjected to heavy usage or extreme conditions, such as automotive parts or outdoor electronics.
Additionally, in injection molding, designers must consider the cooling and shrinkage of materials. If the design isn’t properly aligned with how materials contract during cooling, the product may experience dimensional inconsistencies, warping, or cracking. For example, parts with thick cross-sections may cool at different rates, causing stress that could lead to failure over time. By conducting a structural analysis, you can mitigate these risks, ensuring that your product is robust and reliable in the long term.
6. Final Materials Selection
As your design evolves, it’s time to finalize your materials selection. By now, you should have a clearer understanding of which material best fits your product’s needs in terms of cost, performance, and manufacturability. This decision may come after further testing, simulation, or consultation with suppliers.
For example, if you’re designing a medical device that requires sterilization, you might opt for a material like PEEK (Polyether Ether Ketone), which is known for its excellent resistance to heat and chemicals. On the other hand, if you’re designing a disposable packaging product, something more cost-effective like PET (Polyethylene Terephthalate) might be suitable.
7. Modify the Design for Manufacturing (DFM)
Design for Manufacturing (DFM) is the process of refining your design to make it easier, more cost-effective, and more efficient to manufacture. It’s an essential step for anyone looking to move from prototype to production, as it helps ensure that the product can be made without significant delays or unexpected costs.
The DFM process involves analyzing every aspect of the design to identify potential challenges that could arise during production. In the case of injection molding, this might involve simplifying parts to reduce the complexity of the mold. For example, if the design has deep undercuts or complex geometries that make it difficult to eject the part from the mold, these features could be modified or eliminated altogether.
A good example of DFM in injection molding would be the use of draft angles. Without draft angles (slight slopes on the sides of the mold cavity), the molded part might get stuck in the mold, requiring additional labor or tooling to remove it. Draft angles of about 1 to 2 degrees are often used to facilitate easy ejection. In addition to draft angles, gate and runner systems (which direct the flow of molten material into the mold) are also optimized during the DFM process. By strategically placing the gates and ensuring a uniform flow of material, manufacturers can reduce cycle times and material waste, which in turn lowers production costs.
Another important DFM consideration is part count. The fewer parts a product has, the easier and less expensive it is to manufacture. Consolidating components, where possible, or designing for multi-functional parts can help reduce manufacturing time, tooling complexity, and assembly costs. Ultimately, DFM is about striking the right balance between design complexity, manufacturability, and cost efficiency.
8. Prototyping
Prototyping is where the rubber meets the road. Until this stage, your design exists only as an idea or a digital file. The prototype is the first time you’ll see and feel your design in the real world. It’s an invaluable step for identifying issues that may not have been apparent during the design phase and for verifying that your design works as intended before moving into full-scale production.
For injection-molded products, prototyping often involves creating a limited-run mold that’s used to produce a small batch of parts. These parts are then tested for functionality, fit, and finish. This stage provides a chance to evaluate the product’s real-world performance, including its strength, ease of assembly, and user experience. If you’re working on a consumer product, like a new mobile phone case, you may also want to test for tactile qualities—how does the product feel in hand? Is it too bulky, too slick, or uncomfortable to use?
In some cases, rapid prototyping methods like 3D printing are used to create a prototype. While 3D printed prototypes can help visualize the form and fit of a design quickly, they typically don’t replicate the material properties or production processes of injection molding. However, 3D printed models can provide invaluable insights into design adjustments that are necessary before creating more expensive molds.
Prototyping also offers the opportunity to refine the assembly process. Can all parts be easily assembled? Is there an easier way to connect them? Are any adjustments needed in terms of part tolerances? Testing with a prototype helps uncover these small but significant issues that might lead to bigger problems during mass production.
9. Tooling
Tooling is arguably one of the most expensive and time-consuming stages of product development. This step involves creating the molds or tools that will be used to produce your product in large quantities. The tooling process involves crafting precise molds for injection molding, die casting, or other manufacturing techniques, and it sets the stage for mass production.
Creating the right tooling is essential to the success of your product’s manufacturing process. If the tooling is inaccurate or poorly designed, it could lead to defects such as poor surface finish, dimensional inaccuracies, or excessive cycle times. For injection molding, the creation of the mold is a highly specialized task that requires experienced engineers and machinists. The mold design process considers the number of cavities (how many identical parts can be produced at once), gating systems (how the molten material enters the mold), and cooling channels (to control the temperature and ensure uniform cooling).
The tooling process often begins with prototyping the mold itself, creating test molds to verify the design and identify any issues before full-scale production begins. Once the mold is ready, it undergoes testing to ensure that it’s capable of producing consistent, high-quality parts without excessive wear. For example, if you’re designing a component for an automotive application, you’ll need tooling that can handle high volumes without degradation of precision. Typically, this tooling is made from hardened steel to withstand the pressure of multiple injection cycles.
It’s important to note that tooling costs are a significant part of the overall manufacturing cost, and these costs can vary depending on the complexity of the product design. Complex features, like multi-cavity molds, may cost more to produce but result in faster cycle times and lower per-unit costs. Additionally, if the tooling is designed poorly or needs frequent maintenance, it could lead to delays in production or increased scrap rates, which ultimately raises the cost of production.
10. Production
Finally, we arrive at the production phase, where your product comes to life in large quantities. During production, quality control is key. For injection molded parts, this means checking each batch for defects such as short shots (incomplete filling), warping, or sink marks (surface imperfections due to cooling).
At this point, you’ll likely enter into a continuous feedback loop with the manufacturing team, ensuring the process stays on track. If you’ve followed all the previous steps carefully, the production phase should run smoothly. But even then, regular monitoring is essential to maintain the quality and integrity of each batch.
In conclusion, successful product development is a journey that requires meticulous planning and careful execution. From defining your requirements to final production, each step in the design process plays a critical role in ensuring your product not only meets customer needs but is also manufacturable and cost-effective. By following these 10 key steps, you’ll set yourself up for success and avoid common pitfalls that can derail product development. Take each step seriously, and you’ll be well on your way to turning your ideas into reality.
Materials | Plastic manufacturers often select a standard grade of plastic for a similar application or based on supplier recommendations. However, these resins may not be optimal. In plastic selection, there are many factors to consider, including: |
---|---|
Heat: The stress created by normal and extreme conditions of use and during the assembly, finishing, and shipping processes. | |
Chemical resistance is a property affecting part performance when solids, liquids, or gases are in contact. | |
Agency approvals: Standards developed by the government or the private sector for properties like heat resistance, flammability, and mechanical and electrical performance. | |
Assemblage: During the assembly process at plastic factory, the plastic is bonded, mechanically fastened, and welded. | |
Finish: Ability of the material to come out of the mold with the desired appearance values, such as gloss and smoothness. | |
Price: The price of resin, costs of manufacturing, maintenance, assembly, disassembly, and other costs to reduce labor, finishing, and tools. | |
Access: The availability of resin from the point of view of the amount required for production of plastic manufacturer. | |
Draft | A draft angle makes it easier to remove a cooled, finished part from a mold . Draft angles are an essential component of injection molding. Minimizing friction during the part release process can achieve a uniform surface finish and reduced wear and tear on the mold at plastic factory. |
An angle of the draft is measured according to the direction of pull. Draft angles of at least 0.5° for the cavity and 1.0° for the core are suggested by most design engineers for parts with sufficient draft. The tool must also be designed with more draft if a textured surface is desired and steel shut-off surfaces. | |
Wall Thickness | The wall thickness of injection molded parts is also an important consideration. An injection molded part from plastic products supplier with a proper and uniform wall thickness is less prone to structural and cosmetic problems. |
Most resins have a typical wall thickness ranging from .04 – .150. Yet, it is recommended that you obtain thickness specifications for your material(s) of choice by consulting with an injection molder/design engineer and plastic manufacturer. | |
Wall thickness should be analyzed during the design process to ensure that parts don’t sink, warp, or become non-functional. | |
Ribs | As ribs are used to reinforce the walls of your injection molded parts without increasing their thickness, they are a valuable component in injection molded parts. Rib design should reduce mold flow length when designing complex parts and ensure that the ribs are appropriately connected to increase the part’s strength. |
Ribs should not exceed 2/3 of the wall thickness, depending on the material used. WIDE ribs may create sinking and design problems. It is typical for a design engineer and plastic manufacturer to core out some fabric to reduce shrinkage and keep the strength. | |
If the height of the ribs exceeds 3 times the wall thickness, this could result in the part being short/unable to be filled. Rib placement, thickness, and length are critical factors in determining the viability of a part in its early design phases. | |
Gate | In a mold part, a gate is a point at which liquid plastic flows into it. Injection molded parts have at least one gate, but they are often produced with multiple gates. Runner and gate locations influence polymer molecules’ orientation and how the part shrinks during cooling. As a result, gate location affects your part’s design and functionality. |
The gate should be placed at the end of a long and narrow part if it must be straight. It is recommended to have a gate positioned in the centre of parts that must be perfectly round. | |
With the input of your plastic manufacturer team, you will be able to make optimal decisions regarding gate placement and injection points. | |
Ejector Pin | Mold ejector pins (located on the B-side/core of the mold) are used to release plastic parts from a mold after being molded. The design and positioning of ejector pins should be considered as early in the process as possible by plastic manufacturers. This is even though they are usually a relatively minor concern in the early design phases. Indentations and marks can result from improperly placed ejector pins, so proper placement should be considered in the early phases. |
Ejector pins are typically located at the bottom of side walls, depending on the draft, texture, depth, and type of material. You might be able to confirm that your initial ejector pin placement was correct by reviewing the design. In addition, you may be able to make further changes to improve production outcomes. | |
Sink | Sink marks can appear on the injection molded plastic part during injection moulding when the material shrinks more in thicker areas such as ribs and bosses. In this case, the sink mark is caused by thicker areas cooling slower than thin ones, and the different cooling rates lead to a depression on the adjoining wall. |
Sink marks are formed due to several factors including the processing method, the geometry of the part, the material selection, and the tooling design. The geometry and material selection of the part may not be able to be adjusted based on its specifications, but there are several options to eliminate sink areas. | |
Sinking can be influenced by tooling design (e.g., cooling channel design, gate type and gate size), depending on the part and its application. The manipulation of process conditions (for example, packing pressure, time, phase of packing, and conditions) can also reduce sink. Further, minor tool modifications (e.g., foaming or gas assist) can reduce sink. It is best to consult your injection molder and plastic manufacturer regarding the most effective method to minimize sink in injection-molded parts. | |
Parting Lines | For more complex parts and/or complex shapes, it is important to note where the parting line is located. |
Having your design shared with your injection molder can greatly influence your finished product’s production and functionality since designers and molders tend to evaluate parts differently. The challenge of parting lines can be addressed in several ways. | |
It’s important to be aware of the importance of the parting line when designing your initial concept, but you are not limited to that. You may be able to locate other possible locations using CAD software and mold flow analysis. When you work with an injection molder, they keep your part end use in mind and help you determine where the parting lines should be placed. | |
Special Features | It is essential to design plastic parts so that mold tools can open them and eject them without difficulty. Injection molds release parts by separating the two sides in opposite directions. A side action may be necessary in some instances, where special features such as holes, undercuts, or shoulders prevent the release from occurring. |
Coring is pulled in a direction opposite that of mold separation as a side action. In some cases, costs may increase due to this flexibility in part design. | |
When designing and developing a product, you (plastic manufacturers )were having the right injection molder, and engineer on your side is essential. You can avoid many issues by working with them. In integrating these elements into your product design process and working with a plastics engineer who has experience with these materials, your goal will be to get your product to market as quickly and cost-effectively as possible. |