To optimize entire injection molding manufacturing process, Design for Manufacturability (DFM) is recognized as an effective approach that integrates engineering and production during the plastic design stage to yield high-quality products that satisfy regulatory mandates at reduced cost for end-users.
One key aspect of DFM lies in performing concurrent FMEA and extensive analysis on plastic components towards assessing risk probability – this massively helps maximize all attainable benefits from practicing DFM early enough during product development processes.

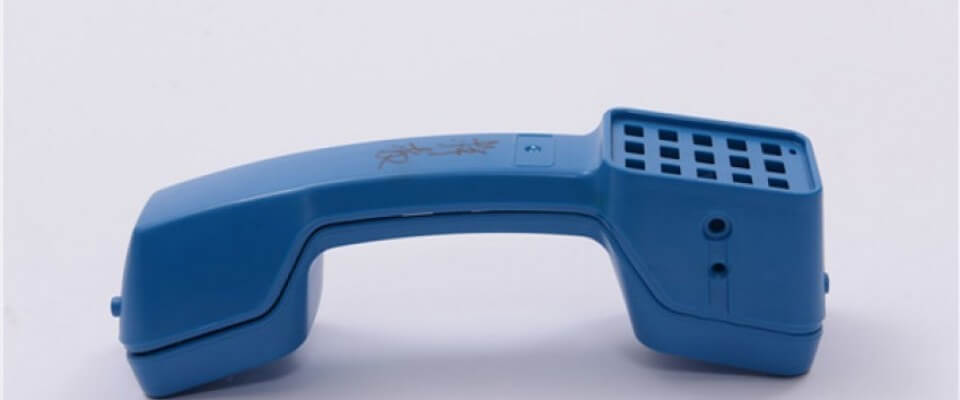
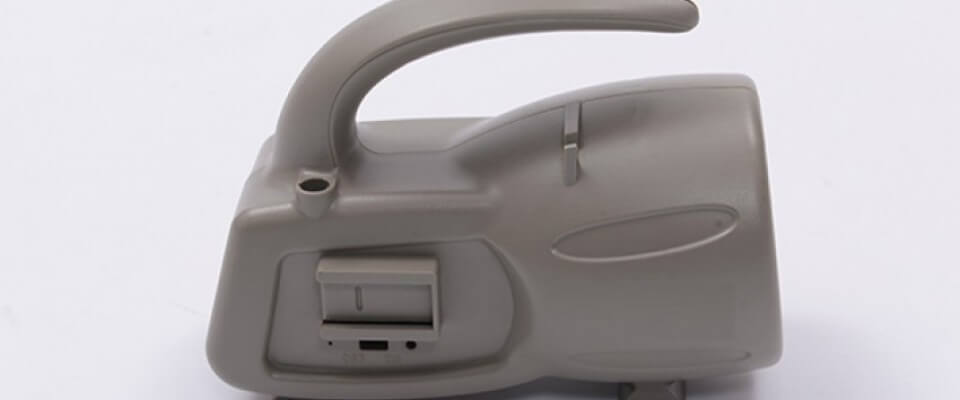
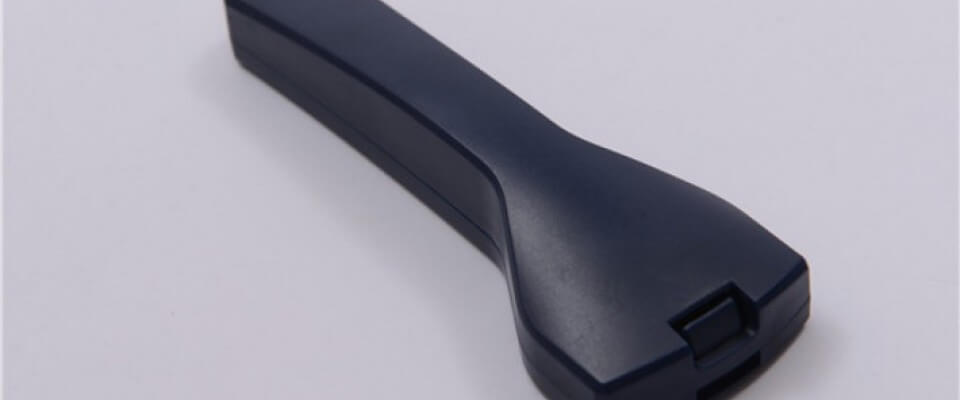
Intricate cases of applying DFM require technical competence in injection dressing skills that fuse well with other techniques like FMEA for an even better outcome – partnering with a qualified DFM-based injection molder adds even more value too! Detailed designs have considerations made with shape and tolerance in mind before advanced systems or standards get integrated.
Establishing the right tolerance level for a part depends on how it functions – anticipating potential failures and adopting methods to prevent them proactively can lead to significant cost-savings in both money and time.
Therefore, employing performant FMEA-based risk assessments is crucial towards early identification of problems and efficient problem-solving methods.
FEEDBACK ON THE DESIGN PROCESS IMPROVED
When it comes to detailed design, shape and tolerance are two key considerations. Shape is only relevant when advanced systems or standards are involved. In order to establish tolerance one must assess how it impacts the function of a particular part.
Taking a proactive approach to failure prevention can help reduce both time and costs by anticipating issues during the design process or plastic part analysis.
The ultimate goal is to design and manufacture reliable products that meet all required specifications. By evaluating, documenting, and prioritizing corrective actions based on failure modes engineers can use FMEA to optimize product performance during the design phase. Through DFM methods – with FMEA being particularly effective – risk probabilities can be controlled during the design phase.
PROCESS CAPABILITIES ALIGNED WITH TECHNICAL SPECIFICATIONS
This builds confidence at every stage of the process from conception through completion.
Analyzing plastic flow and cooling during injection molding requires tool simulation software.
Understanding how plastic behaves within the tool is critical for ensuring that part design elements such as wall thickness, draft, gate locations, geometries etc. are appropriate.
Many software options exist for this purpose with each project requiring selection according to specific requirements so as to enhance production efficiency while also improving overall quality.
TOOL BUILD: REDUCED CHANGES
DFM analysis reduces costs by managing tool build changes post tool build stage. Engineers can use test results obtained previously in order to help manufacturers reduce costs and save time by addressing potential issues early on during planning stages.
In order to minimize changes after toolbuild stage is completed and maintain maximum efficiency practical solutions must be sought out quickly when potential project stumbling blocks occur during initial planning phases.
FABRICATION WITH LESS COMPONENTS, AT A CHEAPER PRICE, AND WITH FEWER COMPONENTS
When attempting automation cost reduction efforts, using fewer components is key in reducing material requirements and ordering frequency which consequently lowers costs incurred in performing these operations. This efficient approach also makes inventory management more manageable for end-users while enhancing their field service experiences too.
DFM simplifies fabrication by substituting materials which in turn strives toward lowering costs while improving series of processes such as assembly process fluidity along with optimizations achieved through proper geometry formation enhancing general part quality at an economical price.
WHO GETS THE MOST OUT OF DFM?
The versatility of DFM means it is appreciated by various business specializing across diverse fields although its most significant value derives from its upfront evaluation during new product development life cycle.
For lack-of-experience designers working on plastic parts designs, partnering with injection molders possessing professional skills greatly enhances their communication ability by providing access to expert level knowledge combined with cutting-edge technology enabled results-driven solutions.
DFM-Based assessments also help in estimating final cost per part and overall manufacturability, culminating in optimized design schema to establish an efficient production schedule. Understanding the importance of “Sweet Spot” during design reviews which are done through detailed 3D models (CAD files) expedites the DFM analysis process.
DFM GUIDANCE FROM TOPWORKS – WHY?
Whether you belong to the medical industry or automotive sector or any other industry type seeking product solutions, it is important to conduct a DFM study by a certified injection molder. This study helps immensely by providing upfront feedback resulting in meeting project specifications while keeping cost-control intact.
Our at Topwoks’ approach towards DFM analysis is collaborative rather than just being an exhaustive process that achieves no solution-focused outcome. We pride ourselves on our multi-disciplinary approach with an experienced team comprising of toolmakers, manufacturing engineers, coordinate measuring machine (CMM) technicians as well as quality & design engineers for plastic parts all working collaboratively while striving towards desired outcomes for clients’ products using this method along with our strong experience in DFM solutions including FMEA analysis.