shrinkage
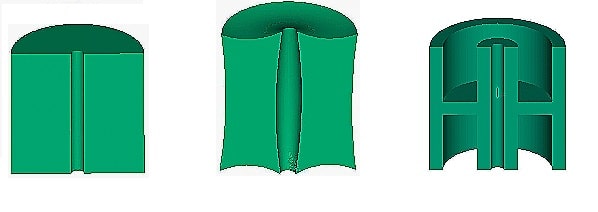
It is important to recognize that each plastic has its own inherent characteristics. A molded piece shrinks after being formed in the mold, which is called shrinkage.
Plastic shrinkage is one of the most common defects in injection molding. It can lead to warpage, sink marks, and other issues that ruin part quality. Controlling shrinkage requires careful consideration of material selection, process settings, and mold design. This guide examines the factors that impact shrinkage and proven methods to minimize it.
What Causes Plastic Shrinkage in Injection Molding?
Both designers of molded products and designers of molds should understand shrinkage’s fundamentals, even though mold designers’ concerns about shrinkage are greater.
As a result of a change in the linear dimensions of the mold and the molded piece, at room temperature, shrinkage must be calculated.
A phenolic generally shrinks between 0.001 and 0.015 inches. Per in., based on how thermosetting plastic is manufactured, the material from which molds are produced, and the conditions under which pieces are made.
It shrinks by 0.050 inches of polyethylene thermoplastics. Per in.Despite being well known and compensated for, in general, plastic shrinkage characteristics, having adequate data to predict accurate shrinkage within various sections of a molded piece can be difficult.
There are many variables and combinations of variables that require study to properly understand shrinkage, which is why technical knowledge is still insufficient.
In general, shrinkage is caused by one or a combination of the following factors, and the extent to which a piece will shrink is determined by one or a combination of them:
Plastic shrinkage occurs because polymers expand when molten due to the energy imparted during processing. As the plastic cools in the mold, it contracts. The amount of shrinkage depends on:
The Type of Plastic
Amorphous plastics like ABS, PC, and PMMA shrink more than semi-crystalline plastics like PET, HDPE, and PP. Thermosets like epoxy and silicone can shrink upwards of 5% from the hot plastic state to room temperature. High filler loadings and reinforcements like glass fibers also constrain shrinkage.
The Melt Temperature
Higher melt temperatures decrease the viscosity, allowing the polymer chains to spread out more in the barrel. Subsequent cooling and crystallization in the mold lead to increased shrinkage. Any process changes must balance fill/pack with minimizing material heat history.
The Mold Temperature
Lower mold temperatures lead to frozen off flow fronts and localized packing, increasing residual stresses. However, higher temperatures also increase cycle times. The best option is using the highest temperature that maintains part quality and economic cycle times.
The Injection Pressure
Higher injection pressures result in more melt momentum and molecular orientation as the plastic fills the cavity. This ultimately causes greater shrinkage as molecules relax during cooling. Balancing fill with limiting orientation helps control shrinkage.
The Packing Pressure
Increasing packing pressure and time allows the plastic to pack out closer to the tool walls. This reduces sinks from shrinkage but can also increase residual stresses. Tuning the process to use the minimum required pressure is key.
The Cooling Time
Faster cooling “freezes” molecules in an expanded state before full relaxation. Slower cooling allows more uniform contraction and stress relief. The cooling time should allow sufficient crystallization for dimensional stability but avoid residual stress buildup.
Carefully selecting the material and tuning the above injection molding process settings helps minimize shrinkage. However, further control requires mold technologies that account for plastic shrinkage.
Tips for Controlling Plastic Shrinkage in Injection Molding
Mold designs and post-molding processes can overcome the challenges of plastic shrinkage:
Use a Mold with a Conformal Cooling Cavity
Conformal cooling channels follow the contour of the mold cavity to ensure uniform cooling. This prevents localized shrinkage that can cause warpage and sink marks. Conformal cooling is only possible with 3D printed molds or CNC machined beryllium copper cavities.
Increase the Melt Temperature
A slightly higher melt temperature reduces viscosity and allows better flow of the polymer. This enhances packing out in the mold and lowers stresses from flow induced orientation. However, too high of a temperature can decrease cycle times and part quality.
Lower the Mold Temperature
Cooler mold surfaces promote faster freezing off, which maintains the expanded plastic state. However, drastically lower temperatures can also lead to flow marks, sinks, and warpage. As a general rule, start with a mold temperature around 60-80°C.
Increase Injection Pressure
Faster injection promotes better cavity filling before solidification begins. The increased pressure packs out the plastic, lowering voids from shrinkage. Care must be taken to avoid excessive orientation from high shear rates.
Optimize Packing Pressure and Time
Higher packing pressure applied over a longer time allows the plastic to relax and conform to the mold walls. This compensates for volume loss from shrinkage. Too much pressure risks residual stress. Packing should only be increased where sinks are visible.
Allow Sufficient Cooling Time
Longer cooling gives molecules more time to crystallize and contract uniformly. Fast cooling leads to a frozen state and localized shrinkage. Allowing cooling time is especially critical for thicker parts. Cooling is complete when ejection temperatures are below the heat deflection temperature.
Maintain a Consistent Process
Shrinkage is sensitive to any process fluctuations. This includes inconsistencies in temperatures, pressures, cooling, or cycle times. Use automatic process monitoring and cavity pressure sensors to detect changes and compensate via the machine controller.
Account for Shrinkage in Part and Mold Design
Building shrinkage into the CAD model helps prevent distortion in the final product. Common techniques include adding draft angles, designing uniform wall thicknesses, and using ribs for structural stability. The mold can also offset shrinkage with expansion cores, machining in shrink factors, and texturing to hide sinks.
The Impact of Plastic Shrinkage on Part Quality
Understanding plastic shrinkage is critical because it drastically influences the final part quality:
- Warpage – Uneven shrinkage through the part thickness causes warpage and distortion after demolding. Maintaining uniform cooling and wall thicknesses helps avoid warpage.
- Sink Marks – Sinks happen where plastic cannot pack out enough to compensate for shrinkage. This occurs around bosses, ribs, inserts, gates, etc. Increasing packing pressure and slowing cooling minimizes sinks.
- Cracks and Voids – The plastic pulls apart or cavitates as molecules contract with insufficient relaxation time. Allowing cooling time for stress relief prevents cracking and shrink voids.
- Poor Dimensions – Overall shrinkage causes undersized parts if not accounted for in tooling dimensions. This makes precise size control difficult.
Controlling plastic shrinkage is crucial for producing high quality, durable plastic parts at the lowest cost. This requires selecting the optimal material, using robust mold designs, and tuning process parameters to promote uniform packing and stress-free cooling. Simulating shrinkage beforehand using molding simulation software helps validate the design. With the right scientific approach to overcoming shrinkage,injection molders can deliver perfectly dimensioned, flawless plastic components from the machine.
Plastic Material Name | Shrinkage Ratio (%) | Plastic Material Name | Shrinkage Ratio (%) |
---|---|---|---|
Acrylonitrile Butadiene Styrene (ABS) | 0.4 〜0.9 | Acrylonitrile styrene (AS) | 0.2 〜0.7 |
Polystyrene (PS) | 0.4 〜0.7 | Ethylene vinyl acetate (EVA) | 0.7 〜1.2 |
Poly Propylene (PP) | 1.0 〜2.5 | Poly Propylene (with 40% glass fibers) | 0.2 〜0.8 |
High-Density Polyethylene (HDPE) | 2.0 〜6.0 | Methacrylic Acid Methyl Ester (acrylic) PMMA | 0.1 〜0.4 |
Polyamide (Nylon 6) | 0.5 〜1.5 | Polyamide (Nylon 66) | 0.8 〜1.5 |
Poly Acetal (POM) | 2.0 〜2.5 | Poly Butylenes Terephthalate (PBT with 30% glass fibers) | 0.2 〜0.8 |
Polycarbonate (PC) | 0.5 〜0.7 | Poly Phenylene Sulfide (PPS with 40% glass fibers) | 0.2 〜0.4 |
Liquid Crystal Polymer (LCP with 40% glass fibers) | 0.2 〜0.8 | Modified Polyphenylene oxide (Modified PPO) | 0.1 〜0.5 |
Poly Sulfone (PSF) | 0.7 〜0.8 | Polyether Sulfone (PES) | 0.6 〜0.8 |
Poly Ethylene Terephthalate (PET) | 0.2 〜0.4 | Polyether Ether Ketone (PEEK) | 0.7 〜1.9 |
Fig. 12-1