Plastic material selection determines the final dimensions of injection molded parts through the manufacturing process
The injection molding process serves as a preferred manufacturing method to produce precise plastic elements with repeated results. Engineers together with manufacturers struggle to achieve precise final dimensions of molded parts as a primary manufacturing challenge. The plastic material selection strongly influences the final dimensions of injection molded parts because of its natural characteristics alongside processing response.
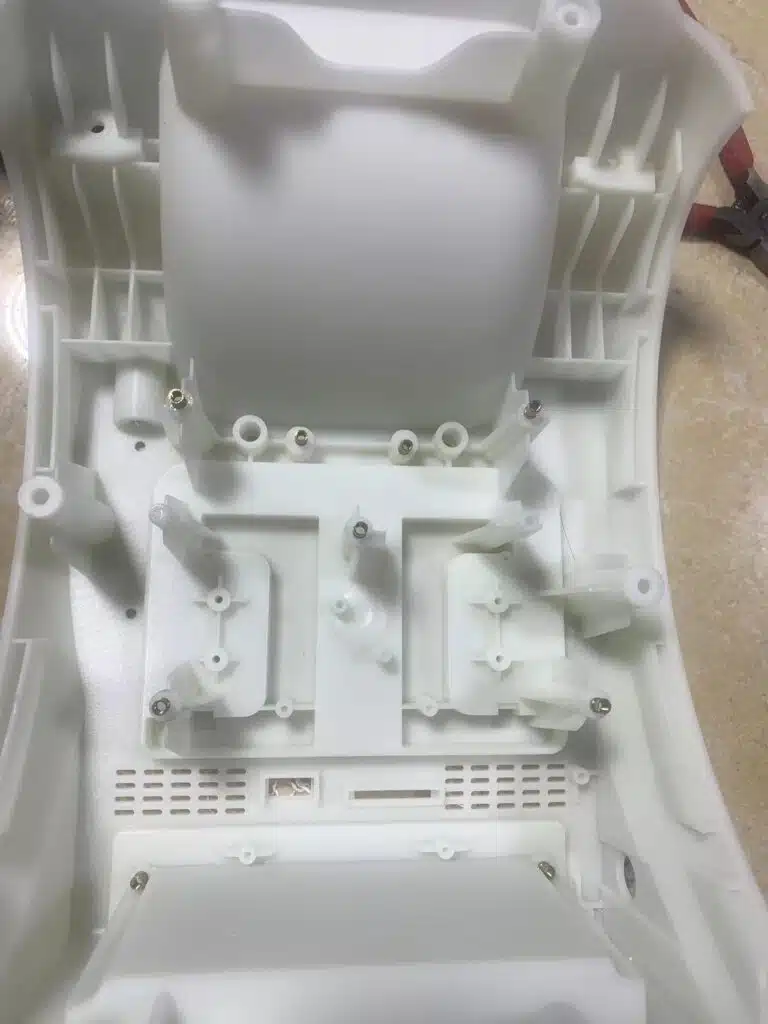
Molecular Structure and Shrinkage Behavior
Various plastic materials display different molecular arrangements which determine their cooling shrinkage amounts. The plastic material classification divides into two groups: semi-crystalline and amorphous types. Semi-crystalline plastics consisting of polypropylene (PP) and polyamide (PA) possess molecular arrangements which form crystals when cooled. Plastics with semi-crystalline structures experience greater dimensional changes than polystyrene (PS) and acrylonitrile butadiene styrene (ABS) because the crystallization process in semi-crystalline materials causes more substantial volume reduction.
The dimensional changes result from volume reduction which occurs when semi-crystalline materials align their polymer chains tightly for packing. Shrinkage in amorphous materials remains minimal since they lack crystalline organization but manufacturers must handle other dimensional stability requirements throughout design development.
Material-Specific Shrinkage Rates
Mold designers need to consider specific shrinkage ranges of each plastic material when developing their designs. The shrinkage rate of HDPE falls between 1.5% and 4% while nylon 6/6 experiences between 0.7% to 3% contraction. The shrinkage rates of ABS and polymethyl methacrylate (PMMA) fall below 2% because of their low rates.
Shrinkage reduction occurs when glass fibers are incorporated as fillers because these elements limit the movement of polymer chains. The need for strict dimensional tolerances makes glass-filled materials the preferred choice for such applications. The correct design of molds and final dimensions of parts demands knowledge about the unique material-specific shrinkage rates of each material.
Directional Shrinkage and Flow Effects
Shrinkage affects different directions of a material at varying rates thus complicating the process of dimensional control. Molten plastic entering the mold cavity produces chain orientation which results in dimensional distortion that is not symmetrical. Flow-aligned amorphous materials exhibit more dimensional shrinkage than semi-crystalline materials which tend to shrink more opposite to the flow.
When designer fails to account for fiber alignment direction in mold design the resulting fiber-reinforced plastics show reduced shrinkage along that direction and this can lead to warping effects. Particular attention should be paid to this directional shrinkage effect during the design of parts that require specific dimensional specifications at particular orientations.
Influence of Molecular Weight and Additives
The pressure required to properly fill molds increases as the polymers achieve higher molecular weights because their melt viscosity becomes higher. An improper pressure compensation method will result in additional shrinkage together with inaccurate dimensions.
The addition of pigments and nucleating agents modifies crystallization flow patterns along with affecting shrinkage levels in plastic materials. Certain additives in products function as crystal nucleation centers thus affecting both total dimensional reduction and orientation of shrinkage patterns. The correct comprehension of material interactions helps predict the dimensions of final parts.
Processing Conditions and Their Impact
Processing parameters which include melt temperature and mold temperature together with injection speed and cooling rate have substantial effects on the final dimensions of produced parts. Shrinking becomes more pronounced at higher mold temperatures because the cooling process slows down and the crystallization expands throughout the material. Rapid cooling helps diminish part shrinkage yet produces stresses within the material which might result in dimensional problems later on.
The dimensions of final parts heavily depend on both injection pressure and packing pressure. When packing pressure is elevated it minimizes shrinkage because it pushes additional material into the mold cavity while the part cools. The achievement of proper dimensional control requires finding precise processing parameter settings.
Design Considerations for Dimensional Accuracy
The design elements in parts such as wall dimension and rib pattern influence both cooling speed and dimensional changes during the manufacturing process. Parts made from thicker regions take longer to cool down and contract more which may result in sink marks or warped structures. Strategic rib placement combined with uniform wall thickness reduces material problems that lead to better dimensional stability.
The position and style of gates determine how materials enter the mold and subsequently how they contract. Strategically placed gates serve to distribute flow evenly throughout the part while minimizing differences in shrinkage between areas.
The process of accounting for material shrinkage during mold design phases
Mold designers include shrinkage allowances in their designs based on the precise data concerning material shrinkage properties. The amount of allowance depends on both the direction and shape of the part. The modern simulation software predicts material shrinkage and warpage behavior so designers can optimize their designs before producing the mold.
Prototype molding with repeated testing is key for complex parts and difficult materials because it allows designers to hit their dimensional targets.
Injection molded plastic parts finalize their dimensions as the material interacts with the process conditions while the part design is the deciding factor. Understanding how different plastic materials shrink during manufacture enables you to make parts that require tight tolerances. Manufacturers who choose the right material, optimize the process parameters and include mold design with shrinkage compensation can minimize defects and meet performance specs.
Engineers and manufacturers benefit from this information when they work to improve the quality and consistency of parts made via injection molding.