Injection molding is the most common plastic manufacturing method. It is used to produce large numbers of identical plastic parts from a single molding machine. It can also be used to make small batches of non-identical parts if the injection molds are specially designed for that purpose.
Injection molding is a process by which molten plastic is injected into a mold, where it cools and solidifies. The molds are made of metal or plastic and come in a variety of shapes and sizes.
The injection molding process begins with the melting of the plastic material in an injection machine, which uses heat to soften the material. The melted plastic is then forced through a nozzle into the mold cavity. When the material enters the mold cavity, it cools and solidifies as it meets resistance from the walls of the cavity. Once cooled, the parts are ejected from the mold cavity by mechanical ejectors.
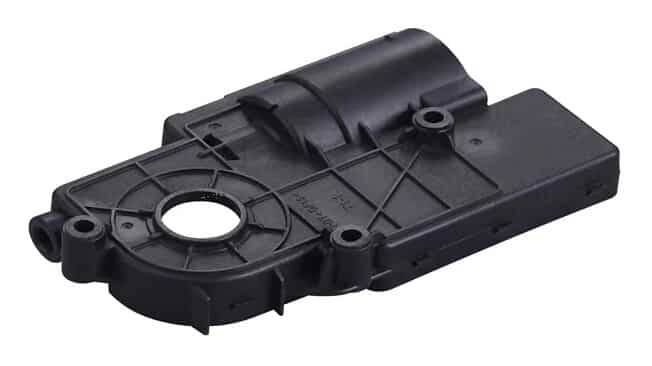
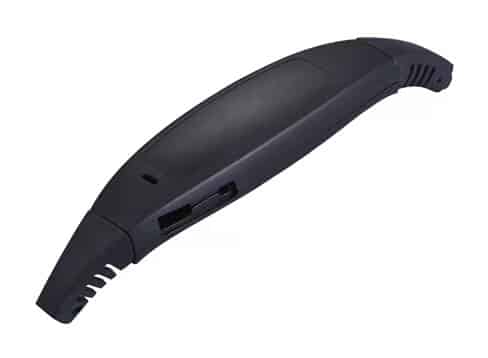
What can injection molding do?
Injection molding is a manufacturing process used to produce a wide range of products. Injection molding can be used to make plastic parts, metal parts and ceramic parts. It is also used to make many everyday products that you may use on a regular basis.
There are many benefits to using injection molding machines for your business needs. Some of these benefits include:
-Increased efficiency – Injection molding machines can produce hundreds of thousands of parts per day, which means they can produce large quantities quickly and efficiently without compromising quality or precision in any way.
-Higher quality
The precision required by injection molds allows them to create parts with high levels of detail and accuracy, meaning they can be used for both consumer goods as well as industrial applications where accuracy is critical (such as medical devices).
-Lower costs
Because injection molds can produce so many parts at once without compromising quality or precision, businessescan save money on the cost of production and shipping.
-Environmentally friendly
Injection molding machines are much more energy efficient than other manufacturing processes, which means they create fewer greenhouse gases and waste products that are harmful to the environment.
Mould design
Mould design is an integral part of the injection molding process. It’s a complex process that requires experience and expertise to do it properly. If you’re not familiar with the intricacies of mould design, outsourcing this part of your project may be advisable.
Mould designers use a variety of tools and techniques to create moulds that will produce parts with high quality and consistency. They often work with engineers who can help them determine how to best incorporate their designs into CAD files so they can be used in CNC machines during production.
There are many different approaches for designing molds, ranging from hand sketches on paper pads up through full-scale 3D models made by computer programs such as Solidworks or AutoCAD Inventor Fusion 360 software online at Autodesk
Injection molding materials
Injection molding uses a wide variety of materials. The most common are: ABS, POM, PC, PP, PE and PVC. Some of these materials can be used in complex molds with multiple cavities to create multiple parts at a time.
In general terms they are categorized into two types: thermoplastics and thermosets. Thermoplastics are materials that can be melted again at low temperatures (generally around 150°C) while thermosets cannot be remelted without degrading their mechanical properties significantly.
Nylon is another example of a thermoplastic that is often used for its strength-to-weight ratio as well as its resistance to flex fatigue and creep under load over time—this makes it ideal for applications where the material needs to survive repeated use like car parts or orthopedic braces (for example).
Injection molding cycle time and cost
Injection molding cycle time and cost are two of the most important factors when you’re buying injection molds online. So let’s dive into them!
Cycle time refers to the time it takes for one cycle of injection molding. This includes the time it takes for the mold to cool down after being injected with molten plastic, as well as the time it takes for the mold to warm up before it can be used again.
The cycle time is the duration for each shot, which includes:
– Preheat (when the screw and barrel are heated to the required temperature)
– Injection (when material is injected into the mold)
– Holding (a period after injection where the pressure inside the barrel is held constant)
– Cooling (when part cools down)
– Ejection (part removal from the machine)
Cycle time is usually measured in seconds or minutes.
The speed of your company’s machine will affect how long it takes to complete an injection molding cycle—the faster the machine, the shorter the cycle will be—so this should also be taken into consideration when comparing prices between different companies.
Injection molding cost depends on:
– The size of your parts (bigger parts require more material and therefore cost more)
– The complexity of your parts (complex parts have more complicated molds and therefore cost more)
Inspection of injection moldings
Inspection of injection moldings
Injection molding is a complex process, and it’s crucial to inspect your product before you seal the deal. Here are some tips:
- Inspect the surface quality of the plastic. Look for any flaws in the finish, such as scratches or chips in the surface. These defects can affect how well your product performs once it’s out on store shelves and they may even impact its safety. If your plastic isn’t smooth enough, it might not grip a handle properly or have edges that are so sharp they cut into someone’s hand when they pick up the item by accident.
- Check for dimensional accuracy. Make sure all dimensions are within acceptable tolerances—for example, if your product has screw holes which need to be drilled into wood before assembly happens later on down at home depot then make sure those holes aren’t too small or too big!
- weight,density, and strength are some of the other important characteristics you can test for. If your product is too heavy, it may be hard for consumers to lift up and hold onto. If it’s too light, then it might not be strong enough to withstand regular use or wear-and-tear over time. And if your product has weak structural integrity, then that can make it prone to breaking easily under pressure!
- chemical composition.Chemical composition is another important thing to test for. If your product contains chemicals that are harmful or toxic, then this can be a problem (especially if it’s going to be used by kids). You might want to research what types of materials are used in other similar products so you can avoid using them too.
Conclusion
It’s easy to see why injection molding is the most popular method of manufacturing plastic products. It offers a high degree of precision and control, as well as flexibility when it comes to designing new parts.
The process also allows manufacturers to produce complex components that would be impossible using other methods (such as casting), while still being able to easily make small batches or prototypes without sacrificing quality or cost effectiveness.
If you need some custom parts made and don’t have time or resources for developing them in-house, then buying injection molded goods online from China might be the perfect solution!