Smart Molding and the Future of Manufacturing
Picture the typical factory floor from past times. The environment of this manufacturing area consists of noisy operations and minor oil stains while workers operate big equipment to produce machine parts by hand. The industrial picture you have in mind remains valid yet understand that digital intricacy will soon form multiple layers of complexity.
Smart Molding introduces plastic injection molding to an Industry 4.0 implementation. The future production floor integrates machines that communicate with each other while streaming real-time data and using predictive analytics methods and robots operate next to human technicians. This modern system delivers exceptional efficiency while representing the future which will arrive powerfully during 2025 and the following years.
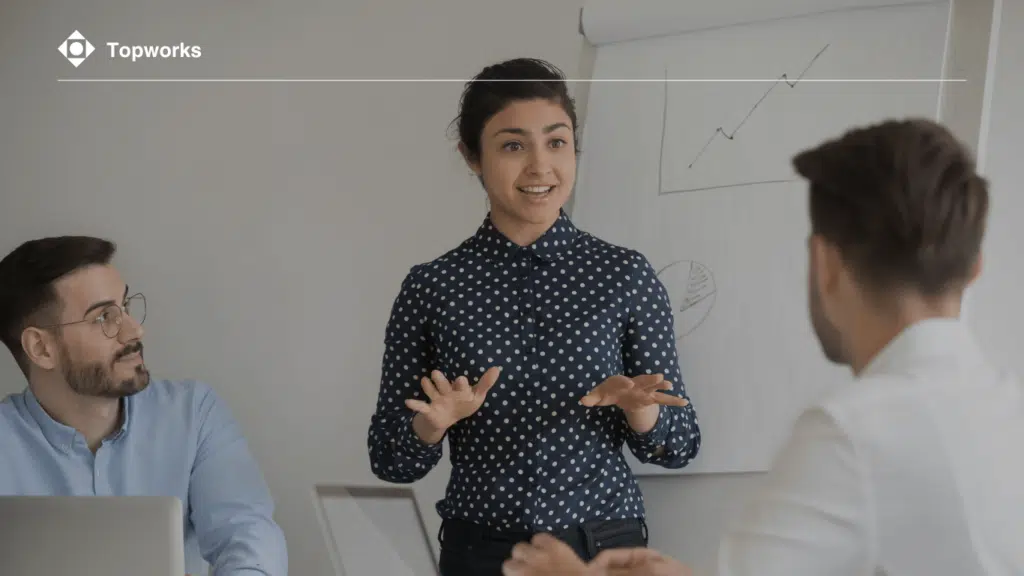
The modern technological advancements have created a substantial difficulty in their path. Past abilities will not guarantee future success in this automated environment. The gap between modern factory requirements and worker capabilities is expanding because smart factories need technologically proficient staff members. The objective of this approach is not to remove workers but to enhance their professional capabilities.
People with experience in polymer and mold design must join forces with experts who understand data science alongside robotics and artificial intelligence principles. The following section explores the implications of this transition along with methods to close the difference between old and new capabilities.
Which specific molding technology elements make it “smart”?
We need to establish basic understanding of “Smart Molding” before we can deal with the skills gap. Injection molding receives its biggest technological transformation to become what we call smart molding. Digital technology applications enable the creation of an autonomous and optimized process that demonstrates intelligence through its operations. Key ingredients often include:
- Machines along with molds receive IoT sensors which monitor extensive data about temperature pressure and cycle times and vibrations and numerous additional parameters.
- All systems maintain direct communication networks that connect machines to robots and quality control systems together with ERP (Enterprise Resource Planning) software. Data flows freely.
- The real progress occurs during the data analytic phase. Software processes the incoming data through analysis to detect patterns while it predicts equipment breakdowns in advance (predictive maintenance) and it automatically modifies process settings to achieve peak quality and efficiency.
- Automation and Robotics systems use robots for operations that include part removal along with packing and assembly functions and automated quality assessments (“cobots”).
- The artificial intelligence and machine learning combination will enable sophisticated quality inspections, specially using machine vision. It simultaneously uses performance data to enhance mold designs.
This approach shifts manufacturers from fixing issues (“The machine broke!”) to making advanced adjustments (“Parameter X data shows we can stop an issue before it appears while increasing yield by 2%”). This breakthrough change the way: how organizations handle productivity along with quality management while providing increased flexibility.
Production Excellence Requires a Combination of Traditional Knowledge with Technological Understanding
Throughout the decades the main expertise of injection molding professionals revolved around understanding how polymers behave while setting up and maintaining molds and troubleshooting issues from experience and performing manual part quality checks. Fundamental understanding of processes remains essential because optimization requires knowledge of what you need to understand.
The requirement for the smart factory extends beyond previous industry standards. Future technicians will excel in operating between physical operations and digital systems to become hybrid experts.
Why the Old Ways Aren’t Quite Enough Anymore
An operator works with a machine dashboard that presents numerous real-time data points and trend graphs. The combination of system data alerts and operator intuition is not enough to detect emerging production issues that the system detects first. Knowing how to modify the melt temperature on its own may not fix a robot arm issue or resolve a vision system detected microscopic defect. The context has expanded dramatically.
The New Essentials: Tech Skills Taking Center Stage
The fundamental aspect of skills deficit exists in this area. We need people proficient in:
Data Analysis & Interpretation: Becoming Data Whisperers
The requirement involves more than achieving PhD-level data scientist capabilities. The ability to decipher data meanings stands as the main objective. Technicians should feel confident in interpreting dashboards and charts to identify both anomalies and patterns that analytics software detects. The production process of Smart Molding produces extensive amounts of data which requires attention. The transformation of data into valuable process improvement solutions as well as predictive maintenance knowledge and quality control applications remains essential. The system requires someone who can determine the reason behind its recommendation instead of performing automated adjustments.
Robotics & Automation: Working with the Metal Colleagues
The worker needs to master robot operation basics and safety protocols alongside maintenance tasks and sequence restarts and jam clearance and may require limited skills for cobot path adjustment and programming. The widespread adoption of robotic systems continues to handle time-consuming manual work and physically demanding operations. The workforce requires both comfort and safety to work alongside robots while ensuring operational correctness and stepping in whenever necessary. Workers transition to become supervisors who work together with robots rather than operating machines alone.
AI Systems & Machine Learning: Understanding the Brains
The essence of this statement involves grasping how AI functions without needing to develop it from scratch. A worker needs to understand how AI-powered vision systems check parts while learning machine learning basics for process optimization and verifying the outputs of these intelligent systems. The importance lies in the fact that workers must understand how AI performs complex tasks because it now controls essential quality control operations. Workers must understand both the situations where they can depend on AI systems and the points where human involvement becomes essential.
Advanced Materials Knowledge: Beyond Commodity Plastics
Smart factories operate with innovative materials such as high-performance composites and bio-polymers as well as recycled materials exhibiting unpredictable properties. Workers need to understand the processing needs and potential problems of specific materials and how they operate with advanced machine control systems. Smart molding systems need to operate at their full capacity when processing these advanced materials because they require stricter control conditions. The material science knowledge needed by workers enables them to maximize the capabilities of smart machines. The workforce needs training to master smart molding technology before operating the automated factories planned for 2025.
Addressing the Skills Gap
Okay, we’ve identified the gap. The actual solution needs clarification. Companies must address this challenge because ignoring it would result in lost competitiveness. It requires a multi-pronged approach:
- The present crew needs both upskilling and reskilling to meet future requirements.
Your workforce consisting of experienced individuals constitutes an essential organizational resource. Smart molding depends on their extensive process understanding which serves as a foundation for the system. The main objective should involve implementing technological expertise at different levels:
- Your organization should provide specialized training sessions about system data interpretation along with basic robot control education for your models and AI tool usage instruction.
- The organization should facilitate training sessions that enable mechanical technicians to understand controls and data systems and vice versa.
- Mentorship Programs: Pair tech-savvy younger employees with experienced veterans for mutual learning.
- Vendor Training: Leverage the expertise of your equipment and software suppliers. Their organization offers top-quality educational resources to their customers.
Cultivating the Next Generation
To recruit new employees manufacturing organizations must demonstrate how the industry now operates at a high-tech level. The implementation of partnerships between education institutions involving community colleges technical schools and universities serves to create suitable curricula. Education programs in mechatronics and data analytics minors should operate alongside smart factory co-op and internship programs. The apprenticeship model stands as one of the best training approaches because it combines practical work experience with formal education. Focus on the exciting aspects of working with robotics along with AI and data-related tasks which will interest students from a digital generation. The organization should establish an environment that supports continuous learning as a vital practice.
The technology continues to advance and therefore the workforce must maintain its ability to evolve at the same pace. Leadership needs to invest company funds in continuous training and development through management buy-in. Educational organizations must make their online learning tools along with training sessions and time for instruction available to all students. The organization should formally recognize employees who take charge of their training by gaining relevant smart factory floor skills.
FAQ: Your Questions Answered
The major obstacle in closing this skills gap presents itself as what?
A: Honestly? The main difficulty stems from both employee attitudes and the implementation of organizational change. The process of getting both employers and employees to learn continuously alongside adopting new ways of working proves more challenging than teaching particular technical skills. Training resource investment presents difficulties for smaller companies.
Smart molding technologies alongside robots are projected to change factory floor employment rather than completely eliminate all positions.
The workforce will not lose its jobs but will undergo changes instead. The number of routine manual jobs will decrease yet more technical roles along with maintenance duties and system oversight responsibilities and interpretation of data and automation collaboration will increase. The transition leads workers from manual work toward knowledge-based activities in their manufacturing areas.
We’re a small-to-medium molding company. Does this technology concern us small-to-medium companies or does it only matter to big manufacturing giants?
A: Absolutely relevant! Various smart factory applications are becoming easier to obtain along with greater scalability options. Small manufacturing companies obtain major competitive benefits through the implementation of smart molding technologies. The trend along with its required skills gap should not be ignored because it will affect companies of all sizes. The initial step should include small-scale improvements such as enhanced data gathering or implementation of a single collaborative robot.
What is my best initial move to prepare for future changes when I already work as a molding technician?
A: Get curious about the data! Observe the data that your existing machines automatically generate. You should inquire about the significance behind data points. Seek out all training sessions your company provides including sessions about new equipment and software systems. Initiate understanding of the process reasons despite focusing only on execution steps. Students should enroll in basic data analysis and IoT fundamentals courses through online education platforms.
Isn’t finding people with all these skills impossible?
It is challenging to identify people who simultaneously excel in molding technology and data science and robotics and AI expertise. The main objective does not require complete mastery from every employee. Team building requires members who possess different abilities while maintaining basic knowledge of technology integration across the team. Staff members should develop T-shaped competencies which include specialized expertise in molding alongside an understanding of adjacent technological fields.
Conclusion: Embracing the Smart Future, Together
The evolution from smart molding to the automated factory of 2025+ represents a fundamental change at the human level. The power of machines together with sensors and software remains limited until operators with skilled expertise use them effectively.
The preparation of the workforce for the Automated Factory of 2025+ represents a strategic business requirement that extends beyond human resources and training department responsibilities for companies in the molding industry which aim to succeed during the upcoming years. The successful implementation of this approach demands financial backing together with educational-industrial partnerships and persistent dedication among people to actively pursue continuous learning. The intelligent and connected molding future needs an efficient workforce which we must prepare to lead this transformation.