Molde de preforma PET, fabricante de moldes de preforma en China
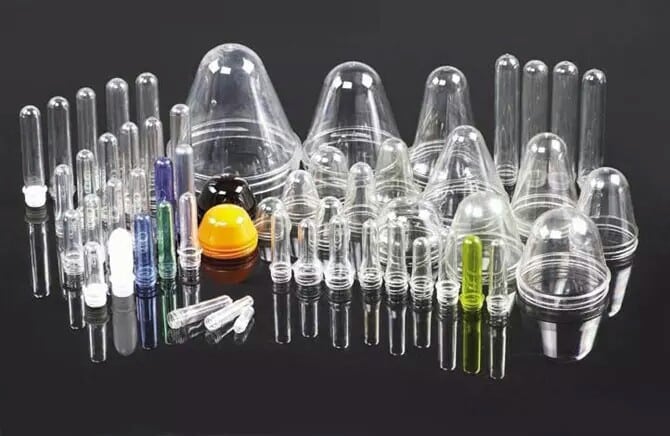
Cómo comprar moldes de preformas de PET: Soluciones de precisión para la fabricación de botellas
Para comprar moldes de preformas de PET de alta precisión, seleccione proveedores en función de su experiencia y de la durabilidad de los materiales y el cumplimiento de las normas del sector. Un buen diseño de molde mantiene tiempos de ciclo rápidos y una calidad de producción estable.
Guía en 3 pasos para adquirir moldes de preformas PET
Empiece por definir sus requisitos de capacidad y número de cavidades solicitando planos CAD a proveedores certificados en [Nombre del producto].
Compruebe las certificaciones ISO 9001 y FDA mientras examina los resultados de las pruebas que demuestran que los moldes de preformas de PET para botellas tienen una tolerancia máxima de 0,01 mm.
La cobertura de la garantía debe incluir componentes de acero resistentes al desgaste que hayan demostrado una durabilidad de más de 1M de ciclos en estudios de investigación.
Molde de preformas de PET frente a la competencia
Factor | Moldes genéricos | [Nombre del producto] |
---|---|---|
Calidad del material | Propenso a la corrosión (6M de vida útil) | Acero cromado (más de 15 millones de ciclos) |
Velocidad de producción | Duración del ciclo 18-22s | Tiempo de ciclo de 12 s (probado) |
Personalización | Opciones limitadas de cavidades | Diseños de 96 cavidades disponibles |
Los usos más comunes de los moldes de preformas de PET incluyen
- Producción de grandes volúmenes de botellas de bebidas (¿Por qué elegir los moldes de preformas de PET en lugar del moldeo por soplado?)
- Envasado médico/farmacéutico personalizado con materiales aptos para la FDA
- La producción de envases ligeros ecológicos pasa por el uso de materiales de PET reciclado que alcanzan un contenido de 30%.
Los moldes PET para botellas de Topworks utilizan 19% menos energía durante la producción de lo que muestran las prácticas estándar de la industria. Seleccione moldes con sistemas de canal caliente con válvula, ya que estos sistemas ofrecen el máximo retorno de la inversión y se adaptan a sus requisitos de producción.
TopWorks es el proveedor líder de soluciones fiables de Moldes de preformas PET a precios asequibles desde hace más de diez años. Nuestro equipo aplica tecnología moderna a materiales de acero de alta calidad (S136,H13) y crea moldes duraderos y rentables que nos han hecho ganar la confianza de clientes locales e internacionales gracias a nuestra dedicación a la satisfacción del cliente.
El trabajo continuo de optimización e innovación de nuestro personal tiene como objetivo producir resultados de calidad excepcional en nuestro proceso de producción. Nuestros moldes para preformas de PET se benefician de los más de diez años de experiencia de TopWorks, lo que garantiza que entregaremos productos que satisfagan los requisitos de nuestros clientes. TopWorks está listo para convertirse en su proveedor ideal de moldes de preformas de alta calidad a precios asequibles.
"¡¡¡Me complace informarles de que todas las piezas de plástico son perfectas!!! Estamos encantados, y por lo tanto hay buenas posibilidades de continuar nuestra relación para cualquier próximo nuevo proyecto."
CRISTIANO
ITALIA
"Steven es un gestor de proyectos e ingeniero muy detallista, capaz de resolver problemas de forma creativa y que además ofrece un servicio excelente. Fue un placer trabajar con él".
DAVID
EE.UU.
Visión general de la fabricación de moldes de preformas de PET de la empresa
Diseño de moldes para preformas PET
- Consideraciones técnicas sobre el diseño
- Configuración del molde (cavidades, disposición)
- Diseño de la puerta
- Sistema de refrigeración
- Sistema de eyección
- Ventilación
- Acabado superficial
- Tolerancias
Materiales para moldes de preformas PET
- Opciones de acero para herramientas
- P20
- H13
- Acero inoxidable 420
- Otras aleaciones
Proceso de fabricación de moldes de preformas PET
- Pasos a seguir
- Diseño de moldes
- Mecanizado CNC
- Tratamiento térmico
- Acabado
- Montaje
- Pruebas y homologación
Nuestro equipo
La mano de obra especializada de Topworks construye y diseña moldes para fabricar características únicas que se adaptan a varios tipos de preformas de plástico PET. Disponemos de capacidades completas para crear moldes de preformas de plástico en todo nuestro agradable entorno de fabricación.
La planta de producción ofrece preformas para la compra que pueden fabricarse para requisitos de envasado individuales mediante la creación de moldes de preformas de PET personalizados. Los clientes pueden adquirir todos los artículos necesarios a través de esta solución completa que opera desde una única ubicación.
¿Cómo se utiliza el molde de preformas PET?
Tereftalato de polietileno (PET) es un polímero termoplástico natural que las industrias utilizan ampliamente en productos plásticos. El GF-PET es el polímero más elegido para las aplicaciones de los clientes, mientras que la inyección de preformas sigue siendo su uso principal. Un material PET líquido presenta propiedades superiores y la presión desempeña un papel más vital que la temperatura a la hora de determinar la viscosidad. En esta situación, la fluidez de la masa fundida depende sobre todo de la presión.
Transformación de plásticos
Los gránulos de PET son muy sensibles al agua durante el calentamiento debido a su naturaleza hidrófila y lipídica. La composición estructural del PET incluye fosfolípidos debido a su presencia. La sustancia pasa a un estado quebradizo junto con cambios de color cuando la concentración de agua supera el límite establecido y hace que el PET pierda su peso molecular.
El procesado requiere una temperatura de 150 °C durante un periodo mínimo de cuatro horas, mientras que el rango típico se mantiene entre 170 °C y tres o cuatro horas antes de que comience la producción.
La cantidad de materiales reciclables debe ser inferior a 25%, mientras que los materiales de cualquier uso necesitan un proceso de secado completo antes de su aplicación.
Máquina de moldeo por inyección
El sistema de inyección necesita elementos de control de la temperatura y un calentamiento de baja fricción, ya que el PET mantiene su forma tras la fusión y tiene un punto de fusión elevado, mientras que el peso del plástico debe ser igual a 2/3 de la dosificación convencional en máquina de un solo disparo.
Diseño de moldes y compuertas
Los moldes de canal caliente funcionan como el equipo para producir preformas de PET. La máquina de moldeo por inyección necesita un material aislante del calor entre ella y el molde de canal caliente. El grosor de las preformas alcanza los 12 mm y los aislantes deben soportar elevados niveles de presión.
Una profundidad excesiva de 0,03 mm en la ranura de ventilación provocará la aparición de destellos.
Temperatura de fusión
Utilizando el método de inyección al aire, el intervalo de temperatura adecuado va de 270 a 295 °C. El mejor intervalo de temperatura para el GF-PET de grado mejorado se sitúa entre 290 y 315 grados Celsius.
Velocidad de inyección
La coagulación del material puede evitarse cuando el proceso de inyección dura de 2 a 4 segundos. La inyección a alta velocidad provoca la fragilidad del material. La inyección dura 4 segundos.
Contrapresión
La presión de inyección debe permanecer por debajo de 100 bares, ya que este nivel ofrece el mejor rendimiento para mantener el proceso.
Horarios de residencia
La degradación molecular se evitará si se mantienen temperaturas inferiores a 300 °C y tiempos de permanencia inferiores a 15 minutos. El proceso de limpieza mediante chorro de aire de la barrica no debe superar los 15 minutos de tiempo de funcionamiento, pero si se requiere una mayor limpieza, utilice PE viscoso mientras se reduce la temperatura de la barrica a la temperatura de PE.
Otros
Debe evitarse el uso excesivo de materiales reciclados, ya que podría afectar negativamente a la plastificación. La niebla blanca junto con el aspecto opaco pueden surgir de temperaturas de molde no controladas.
Por qué un sistema de canal caliente valave para moldes de preformas PET
El precio inicial y la entrega suelen ser factores determinantes en la preforma moldeada por inyección actual. Como resultado de este tipo de adquisición de moldes de PET, las piezas moldeadas no tendrán su ventaja económica a largo plazo para las empresas que producen la primera generación de piezas. Al mismo tiempo, ni siquiera los moldes de tirada corta contribuirán equitativamente a los beneficios finales. Los moldes se modifican a menudo cuando los moldeadores fabrican una nueva generación de la misma pieza básica, creyendo que al hacerlo, la producción de preformas de pPET tendrá tanto éxito que la competencia no ganará el contrato. Un competidor con moldes de producción de piezas a largo plazo, que tienen el mejor retorno de la inversión en comparación con una tirada de producción, estará en una posición más fuerte en la nueva licitación, especialmente si los mismos procedimientos reflejan la perspectiva de toda la empresa.
A la hora de seleccionar un sistema, tenga en cuenta estos factores
La preforma de PET moldeada por inyección, ya sea a corto o largo plazo, debe evaluarse a partir de los puntos que se indican a continuación. Al seleccionar un sistema de inyección, deben tenerse en cuenta todos los aspectos de una operación de moldeado de preformas de PET económicamente rentable: su coste, los costes de las pruebas, los tiempos de preparación, los tiempos de ciclo, el mantenimiento, los desechos, las operaciones secundarias, los equipos auxiliares y la calidad de sus piezas. El tamaño del molde aumenta con el canal y el desplazamiento de la cavidad respecto al casquillo del bebedero en un molde de casquillo frío y cavidad única con inyección en el borde de la pieza. Con sistemas bien diseñados, la resina se desplazará al desplazamiento con el mínimo aumento del tamaño del molde de preformas de PET mediante un canal caliente de perfil bajo.
Los costes del canal caliente se compensan con la reducción del tamaño del molde de preformas de PET
Aunque se reduzca el tamaño del molde de preformas PET, puede compensarse el coste inicial del canal caliente, lo que permite elegir el tamaño de la prensa en función de los requisitos de la pieza. La válvula de paso a la línea de partición reduce la cantidad de resina necesaria por disparo, reduciendo así los desechos (bebederos) y el volumen de reafilado necesario. Desde el punto de vista económico, tiene sentido utilizar un canal caliente para sustituir el desplazamiento del molde en todas las piezas de más de 50 g con una vida útil prevista de más de 150.000 piezas. Debido a la costosa base del molde para un sistema de canal frío, el número de piezas puede ser menor cuando la pieza es más grande, pero el coste de los canales calientes seguirá siendo el mismo.
Ventajas del casquillo del bebedero del molde de preformas PET
Moldes que puerta directamente en una única cavidad mediante un casquillo de bebedero presentan varias ventajas con respecto a las cámaras frías. Basándose únicamente en los requisitos de la pieza, el tamaño de la base del molde de PET vendrá determinado por la prensa más pequeña. Al utilizar casquillos de bebedero en frío, se crean bebederos que deben retirarse, dejando marcas que con frecuencia deben eliminarse mediante operaciones secundarias si preocupa el aspecto o la altura máxima del remanente de bebedero. Los casquillos de bebedero calientes se utilizan habitualmente para evitar esto, pero a menudo dejan una marca inaceptable, reducen la ventana operativa y crean tensiones internas en la pieza (alabeo).
Al utilizar un sistema de compuerta de válvula, no se forma una marca inaceptable, se mantiene una buena ventana operativa y la preforma PET recibe la menor cantidad de tensión. Los sistemas de compuerta de válvula suelen requerir un molde más grande para su sistema operativo, tanto en términos de huella del molde como de altura, ya que deben utilizar un canal caliente para desplazar el mecanismo operativo de la línea central del molde, y tienen que encajar un colector y su mecanismo operativo en el molde. La mayoría de los sistemas adecuados lo consiguen sin aumentar la huella del molde de PET y, a menudo, sin afectar a la altura del molde, ya que la compuerta de válvula está situada en la línea central del molde y no requiere un accionamiento externo.
Molde de preformas PET más grande gracias a la cámara fría
El tamaño del molde de preforma suele aumentar cuando se diseñan moldes multicavidad con sistemas de canal frío para que quepan el canal, las guías y los mecanismos, lo que a su vez dificulta la orientación de la cavidad durante el diseño de piezas complejas. Si hay que modificar piezas o si los tiempos de proceso son largos, la ventana operativa del proceso de moldeo se vuelve muy restringida y el alabeo es casi imposible de controlar.
En la fabricación de moldes de tres placas, los niveles de cavitación son elevados, la disposición de las cavidades es óptima y es posible el funcionamiento automático. La incorporación de un sistema de canal caliente con inyección térmica directa en lugar de la construcción de moldes tradicional permitirá utilizar el molde multicavidad de forma más económica: menor superficie de línea de apertura por pieza, menor altura del molde, tiempos de ciclo más cortos, menos desechos y mejor funcionamiento automatizado.
Además de reducir los tiempos de ciclo, los canales calientes con válvulas reducen la tensión de la pieza y producen piezas preformadas de mejor calidad. Por el contrario, los nuevos sistemas de canal caliente con compuerta de válvula, que aumentan la altura del molde pase lo que pase y son menos costosos, pueden reducir en gran medida los costes y los aumentos de altura del molde de los sistemas tradicionales de canal caliente con compuerta de válvula, que tienen un efecto perjudicial en la eficiencia económica. Los canales calientes pueden pedirse para toda la mitad "A" menos cavidades con el fin de garantizar mejores plazos de entrega del molde. El tiempo de construcción del molde puede reducirse repartiendo la carga de trabajo entre más instalaciones.
El sistema de canal caliente para moldes de preformas PET reduce costes, tiempo y residuos
Un sistema de canal caliente se ha aplicado a la adquisición de moldes de preformas y ha demostrado ser una forma eficaz de reducir el coste inicial, el tiempo de construcción y los costes operativos de pruebas, preparación, tiempo de ciclo, mantenimiento, desechos y operaciones secundarias, y sin necesidad de ningún equipo adicional. Como resultado, la mayoría de las aplicaciones podrán esperar un nivel de calidad constante. Con frecuencia se especifica un sistema de canal caliente con compuerta térmica o un sistema de compuerta de válvula para producir un diseño de moldeo de alto rendimiento. Con este tipo de máquinas, conseguirá una repetibilidad muy alta entre disparo y disparo, tiempos de ciclo más rápidos, un funcionamiento sencillo del molde y piezas de alta calidad. Los sistemas térmicos y de compuertas de válvula bien diseñados suelen superar a los mal diseñados. Con un sistema de este tipo, se necesita menos altura de molde y menos potencia, además de no necesitar controles externos ni sistemas de alimentación auxiliares.
Casi cualquier adquisición de moldes de preformas de PET debería considerar un sistema de canal caliente debido a las ventajas que proporcionará en general. Para obtener las ventajas necesarias para la producción competitiva de piezas moldeadas por inyección en el mercado actual, las instalaciones de compuertas de válvula deben realizarse según las especificaciones del fabricante. Los sistemas de compuerta de válvula son superiores a los sistemas de compuerta térmica porque todos los componentes están construidos de forma muy sencilla y robusta, a partir de un concepto de diseño simple con el menor número de piezas posible para proporcionar el mejor control de flujo de compuerta.